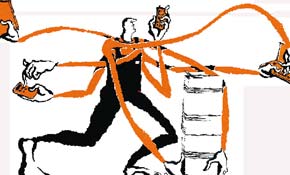
One driver has been the global financial crisis. According to the 2010 Environment Scan from Innovation & Business Skills Australia (IBSA), 54% of printers indicated they had found it necessary to reduce the number of staff over the past 12 months. With fewer staff, many smaller printing companies are now training their workers to be multi-skilled, creating workforces that can move from one machine and discipline to the other.
The printing industry will have to embrace multi-skilling because it’s only getting smaller. Thanks to a combination of falling page volumes and increasingly automated technology, tomorrow’s industry’s won’t need as many bodies on the shopfloor or salesforce. According to estimates prepared by the Department of Education, Employment and Workplace Relations (DEEWR) in 2009, the printing industry is expected to decline in size by 1.8% in the period to 2013-14. DEEWR found that printing industry employment had declined by 8,500 over the previous five years. It is expected to shed another 4,200 jobs in the period to 2013-14.
Running a business with fewer people requires a multi-skilled workforce; it’s the only solution.
Another problem is that the core printing workforce, excluding sales and administration, is ageing. The IBSA report reveals that the industry now has an older average workforce than the wider economy. In 2008, the median age of workers in the printing industry was 42, compared with 37 years across all industries. Simon Cochaud, director of RMIT University’s International Centre of Graphic Technology (ICGT), estimates that the median age of printers will be 47 by 2015 and 52 by 2020. Printing is an age-old industry in more ways than one.
Adding to the problem, and creating more pressure for multi-skilling, is that the industry is not attracting new talent. It has limited attractiveness to young potential workforce entrants. Printing industry employers tell IBSA that print is not seen as widely attractive to young people. Career opportunities within the industry are not understood. Some criticise high school career counsellors, saying they know little about the opportunities in printing and graphic arts.
The printing industry has been slow to respond to these challenges. IBSA found that little formal training occurs in the industry after an apprenticeship has finished. Instead there is more focus on informal on-the-job training, where the individual often has to work things out for themselves.
If they’re lucky, someone will show them or mentor them. IBSA found that 61% of printing and graphic arts companies trained staff informally, only one in three (35%) used fully accredited qualifications, only 6% trained staff using units of competency and 10% provided no training whatsoever.
The key issue for many smaller companies, which comprise the bulk of the industry, would be letting staff take time off work for training. IBSA found that about half the companies (46%) said it was not easy to give staff time for training.
IBSA notes: “The industry has a limited training culture and, particularly in some of the smaller and niche areas, there is a lack of awareness of the availability of relevant qualifications. Many SMEs and operators in niche industry areas do not expect to find external support for their workforce development needs and as a result they don’t take advantage of the public training system.
“Recent economic conditions have prompted a number of large companies to get rid of their training managers and small companies are in survival mode, focusing only on immediate business outcomes,” according to IBSA.
Fewer employees add up to a need for a more multi-skilled workforce.
Another force for change is technology. Modern printing machines are like big computers, and IT skills are one of the areas most lacking across print. However, just because a print shop runs cutting-edge digital machines or sophisticated workflow and MIS tools, the old ways of litho printing and finishing remain essential. Hence cross-training becomes more critical.
Cochaud says smaller companies are now focusing more on multi-skilling since the financial crisis. “We have seen a major increase in it in the last six months. We are seeing
that with more of the companies we speak to,” says Cochaud.
“Employees are multi-skilling their workforce more and they are making their teams become more interdisciplinary, so while they may work in one particular area of the business, they may slip into another area, whether it be for a couple of hours each week or months. You may have someone who is a qualified graphics pre-press person and someone within the company might do some design work and if the designer is called away, then they might do some design work as well.”
RMIT is also training employees to work across different machines. The aim is to produce multi-skilled apprentices, ready for a different type of industry.
Cochaud says there are two reasons companies are taking to training now. The first is financial. State and federal governments have been putting enormous money into training since the global financial crisis with schemes such as the Kickstart pre-apprenticeship training. “Most organisations were holding back on training in the middle of the GFC but we have certainly seen training increase. There are more financial incentives.”
The second reason is demographic. The industry is getting older and it is shrinking. At the same time, the system is producing only 365 apprentices a year in an industry that some estimate still has up to 5,000 print shops. It all points to a massive skills shortage in the next few years. To address this, companies will have to focus on training, recruitment and retention. “While we have seen apprenticeship numbers increase over the past 12 to 18 months and we hope they will continue to do so, we are forecasting that by the year 2015 to 2020, there is going to be a shortfall of 500 to 3,000 qualified apprentices,” Cochaud says.
Ian Walz, national manager learning and development at the Printing Industries Association of Australia, says that more companies are now training their entire workforce on competitive manufacturing.
“They are training not just a few staff, but the whole of the company from management level down to the workers on the floor,” says Walz. “They are training them to go through the competitive manufacturing process and understanding the importance of minimising waste, paper and energy.”
He says more companies are taking to these courses because they are funded by the government. But most, he says, seem oblivious to these opportunities. They either ignore them or they don’t know about them. “I don’t think a lot of employers are aware of the courses available to fill the skills through nationally accredited courses,” he says.
He says more companies are now training staff to work not only across several machines but different departments as well. It is not uncommon to see workers moving from design to pre-press to digital printing.
Another method of creating a multi-skilled workforce is to train salespeople across the entire process. Conversely, account handlers and customer services people can be trained in sales. In this climate, every sale counts, and the more people who can bring in work, the better.
Walz says: “With estimating staff, for example, they want them to have a holistic knowledge not only of the number crunching but also the sale of the product. It’s all about upskilling staff in different areas. What employers want is for people to be able to jump from job to job without too much fuss.”
Still, not all companies are doing this. While the larger printers are more committed to training, the smaller companies are less willing to give employees the time off.
Walz says that many of the larger companies now have specialist positions, particularly around quality and environment. That is inevitable with more print buyers and procurement managers looking for environmental credentials in the products they are sourcing. New job titles appearing at larger firms include ‘sustainability manager’ and ‘quality manager’. But again, there’s that gap between big and small. “A lot of the smaller companies are struggling with the state of the industry at the moment and they are trying to remain afloat but a lot of the larger companies are appointing people to those positions,” Walz says.
He says technology will be the crunch issue for the industry over the next 10 years. But while it might seem that the younger generation is better suited to picking up on new technology, that doesn’t mean the industry’s ageing workforce is incapable of learning new ways.
Walz says most older workers in the printing industry do not have difficulty picking up the technology. “A lot of older workers are becoming more savvy in picking it up,” he says.
John McGuffie, print instructor at Heidelberg, says technology has now become the dominant driver in the print industry. He says many of the older print workers resisted the change many years ago when it was being introduced but times have changed. More are now picking it up, if only because they have no choice.
“Ten years ago, a lot of the older people didn’t take to it. For the people still in the trade, they have to adapt to technology. They must be adaptable. The ones who do that will survive. They need to adapt to technology or they’ll get left behind.”
McGuffie says the computers driving the machines are now standardised according to the brand, whether KBA, Heidelberg, Manroland or Komori. This makes multi-skilling much easier, allowing people to work across different machines.
McGuffie also disagrees that all the big print companies are committed to training. Some are and some aren’t, he says. In the end, he says, it comes down to the manager running the operation and whether they feel that every minute of the employee’s day needs to be taken up with production.
While the GFC and the move to leaner workforces has made multi-skilling that much more necessary, Some companies saw the importance of inter-disciplinary training long before the markets crashed. For them, it’s just makes sense.
IPMG chief executive Stephen Anstice puts it bluntly: “We’ve been doing it forever. Of course there’s multi-skilling but it’s not what I would see as our main focus. It’s like asking me if we use paper. I’m sure, if you’re a smaller printer that’s more the case because there are less people to go around but we have always done it.”
Platypus Graphics managing director Tom Lusch says his company trains printers across all machines. “But that comes about by necessity rather than planning,” says Lusch.
“We are a company that doesn’t run one brand of press. Platypus has Komori, KBA, Roland and Heidelberg. We have bought machinery based on technology rather than brand.
“Most of the printers here, like the printing machinists and apprentices, have their favourite machines and they have the area they work at. But at some point or another, if it’s a big client or we are busy, we move them around. And when we do that, we don’t have this problem where they say they don’t know how to work the machine.”
When it comes to sales people, it’s not a matter of implementing a cross-training strategy. Like many print shops, the sales force has come up from the production floor. “They are normally home grown through production. They learn how to do production and then after 12 months, if they have the ability or the tendency, we will push them into sales.”
Generally, he says his older workers do not have difficulties picking up technology. But when there is a problem, there is a simple solution.
“When you come from the trade side, you go from driving a printing machine to driving a computer. So you put them with someone else. Young people are extremely quick to pick up computerisation.”
The production manager from one of Australia’s biggest printing companies, who did not want to be named, said multi-skilling was a normal part of training. “We do inductions for people and they will spend a day or so in every department of the factory,” he says. “So we will have our retail service people, our estimators and our sales planners all coming through and getting an overview.”
Nonetheless, most of the smaller companies are just treading water, trying to keep afloat. They are reluctant to invest in training. Wayne McDougall, director of training company Skilled Force, says they are signing their death warrant.
“Trying to convince smaller organisations that training can add value to the business can be quite a challenge given that they believe every minute of the employee’s day must be productive with production, and not training,” says McDougall.
Comment below to have your say on this story.
If you have a news story or tip-off, get in touch at editorial@sprinter.com.au.
Sign up to the Sprinter newsletter