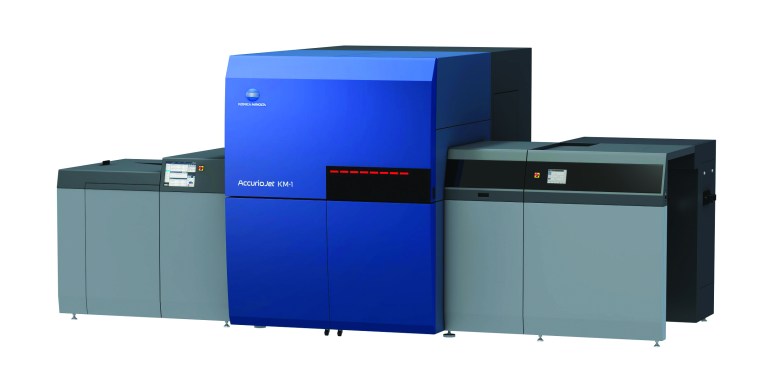
The vendor community has gone a long way with inkjet, both web and more recently sheetfed, and the majors, such as KBA, HP, Konica Minolta and Kodak – to name just some – are positioning themselves as inkjet suppliers in traditional as well as highly innovative market sectors.
In the commercial pressroom, speed and quality do not present the same issues as five years ago. Vaulting the speed/quality gap would of course give inkjet the sprint to the finish line, unencumbered as it is by the analogue phases of prepress, plate prep, and makeready on the press.
Sheetfed inkjet
At Currie Group, the Scodix range has established a firm presence in the Australian market. Bernie Robinson, Currie Group managing director, says the Scodix Ultra range – comprising Scodix Ultra, Scodix Ultra Pro and Scodix Ultra Pro Foil– are the flagship platforms for Scodix, leading sales around the world.
“This second-generation machine comes in three scalable versions that can substitute multiple analogue finishing processes which can all be printed digitally and on a wide variety of media. Its digital nature allows for repetitive, versioned, or personalised unit production; on jobs ranging from one unit to tens of thousands of customised units all imposed in a maximum B2 sheet format (1,250 sheets per hour).
Robinson says, “The Scodix is based on UV polymer proprietary inkjet technology, which can produce finishing effects such as spot low-raise UV, high-raise UV with up-to 99 gloss units that can substitute emboss and braille analogue processes. The fully escalated version of the machine offers foiling and cast-and-cure (holographic film). It is the only solution in the market that can go all the way up to 1,000-micron raised UV effects, known as Scodix Crystal.”
Explaining the business case for Scodix, Robinson says, “These digital printing and finishing solutions remove tooling costs and set-up time that is usual in the analogue finishing world. Unlike any other digital finishing technology, the Scodix platform processes a wide range of substrates from uncoated paper to synthetics, from metallised to black paper or even canvas.
“Scodix is the only digital finishing technology that complements the versatile media demand from any digital CMYK technology, even that of HP Indigo and traditional offset.Additionally, Scodix PAS patented printing technology is the only digital low-heat foiling solution (under around 40°C) of its kind that is gentle with synthetic media, with an incomparable quality which pairs perfectly with HP Indigo’s One-Shot print mode – also focused on synthetic media. Scodix High-build, Spot and Foil are of course variable-data printing friendly.”
Meanwhile, the Scodix E106, which will become available in mid-2019, offers the versatility of the Ultra series, but is able to print in B1 format at speeds of up to 4,000 sheets an hour and with the thickest range of media printable digitally, says Robinson.
“The Scodix Ultra series is focused on the low- to mid-volume general commercial printing sector, while the upcoming Scodix E106 will be focused on the folding-cartons printing sector and alternatively in the high-volume general commercial printing sector,” he notes.
Over at Konica Minolta, Mark Brown, national product marketing manager at Konica Minolta Australia, describes the Accuriojet KM-1 as a UV inkjet B2 size sheetfed press that combines the best of analogue and digital technologies. It prints 3,000 sheets per hour one-sided or 1,500 sheets per hour duplex, all in one pass – no need for work and turn.
“It offers LED curing for the UV inks, allowing for cool curing during the print process,” he adds. “It also does corrections on the fly for any nozzle blocking or deviation to ensure the best possible print quality. The paper path of the press is offset-based, therefore robust, accurate and reliable. As the ink used is UV, there is no need for primers or speciality materials to print onto. Due to the UV curing process, the prints are dry and ready for finishing immediately.”
Brown sees the Accuriojet KM-1 slotting into the commercial pressroom, and says “The value proposition is simple – any commercial print company looking to reinvest in offset or high-end toner or digital technology should put the AccurioJet KM-1 to the test.
“With falling run lengths and increased variable-data requirements, it makes sense.
“The AccurioJet KM-1 is faster than toner and has a wider range of media and applications.
“Although not as fast as offset, the AccurioJet KM-1 combines the same paper path and handling systems as offset and brings the benefit of digital print on top of that.”
Brown adds that the press is suitable for almost all commercial print applications, mail-house applications as well as light folding carton.
Konica Minolta says by integrating litho and inkjet technologies, the KM-1 was built for digital print companies demanding extra capacity, that wish to end outsourcing, but is also seen as a premium solution for conventional offset printers that are expanding into commercial digital printing.
Colin McKenzie, national manager, Inkjet Press Technology for Océ Australia, recounts how over a decade ago Océ unleashed the fastest inkjet press “on the unsuspecting print and mail market”.
“With a market leading presence in toner-based systems, the adoption rate of inkjet far outweighed anything Océ could have dreamt. With market success and recognition came further developments that pushed the known boundaries of print heads, ink dispersal, speed, paper transport and drying – all critical elements in the search for the holy grail.
“Océ has now broken the inkjet code to offer inkjet press technology that produces the best quality that offset can offer and on offset stocks – the two missing elements that have kept the offset printers at arm’s length.
“Océ has spoilt the commercial print market with choices. The first press that meets the offset holy grail is the cutsheet inkjet Océ VarioPrint i300 (VPi300). Océ has delivered over 200 systems into the market, an extraordinary achievement. The second is a web press delivering exceptional quality at very high speeds known as the Océ ProStream 1000.
The VPi300 reflects a genetic makeup of generations of developments, says McKenzie, producing offset quality on offset stocks, one of the major hallmarks of its success. “This press has proven its pedigree in the field with an average uptime of more than 94 per cent, unheard of for a digital press. It is here that the VPi300 separates itself from the digital pack, and closes the gap on offset production. Seeing is believing. Océ and its Australian customers will be conducting open-house events in the near future.”
McKenzie says the Océ VarioPrint i300 (and the ProStream 1000) are “the new offset in every way”. The Australian commercial print market does not have the advantage of larger markets to focus on one or just a few applications, he points out. “In the past, an offset press investment was based on the broadest criteria to deliver a diverse mix of jobs. So it is for a digital press. The new digital press must be versatile, reliable, meet all quality expectations, and above all deliver on the ROI.”
In November, Fujifilm announced its third generation B2 inkjet press, the Jet Press 750S. With higher productivity of 3,600 B2 sheets per hour, and a range of other changes which further improve the already impressive up-time, versatility, colour capability and quality, with the company calling the the Jet Press 750S the fastest, full colour, B2 sheet-fed digital press on the market.
The Jet Press 720S was the first B2 inkjet press to gain a foothold in the market, and had more than 150 installations worldwide. Fujijilm says, “Now with the continued, steady increase in demand for short run work, the introduction of the Jet Press 750S means that more and more jobs are going to fit the sweet spot of this new industry-leading press.
“The target for this press is not the toner-dominated, on demand market where runs of ones and twos predominate. The Jet Press 750S is likely to be highly competitive for print runs up to 5,000, depending on ink coverage, allowing it to compete with, and out-perform, offset presses in the production of high quality, short run print jobs. This makes it an ideal investment for a much larger range of commercial and packaging printers.”
Like the Jet Press 720S, the new press is a blend of old and new technologies. Built on an offset chassis, Fujifilm says it features superb sheet-to-sheet, front and back registration and up-time on a par with offset, combined with Samba inkjet printheads, to deliver quality that the company says outperforms offset.
Heidelberg’s Primefire 106 has been described as the first digital press in B1 format for the packaging market, offering dependable high-quality and industrial production. It combines what it calls the most reliable offset platform in the market, the Heidelberg XL106, with a direct printing process that ensures repeatable high-quality results. It can be plugged and played within an existing workflow by using Heidelberg’s Prinect solutions – all of which are backed by support from the Heidelberg Service Team.
Heidelberg partners with Fujifilm in technology that enables over 12 billion drops per sheet in seven process colours (CMYKOVG), providing around 95 per cent Pantone colour gamut coverage with Heidelberg Multicolor technology. Meanwhile, Heidelberg’s Saphira water-based consumables conform to Swiss Ordinance, offering the best available conditions for low-migration products.
Heidelberg states that the Primefire “can accelerate business growth in a world of increasing short runs, faster turnaround, versioning and personalisation through dependable, high-quality performance”.
Primefire 106 is being introduced in the folding-carton sector, as clamour for versioned and personalised print, as well as short runs and higher supply chain efficiency, is growing fast. At the same time, cost effective production of high volumes is seen as an imperative. Heidelberg says combining its Primefire 106 with traditional offset production provides the optimal mix, offering a printer’s customers the flexibility and consistent quality they need, using proven platforms, working within an established workflow and minimising disruptive integration on-costs.
Webfed inkjet
The presses in Kodak’s Prosper line-up print heavy ink coverage on a wide range of papers, especially glossy papers, and do so at high speed, says Will Mansfield, director of Worldwide Product Marketing & Category Management, in Kodak’s Enterprise Inkjet Systems division.
The range comprises four devices – the Prosper 6000S standalone press, for one-sided printing, the 6000S hybrid (one-sided), and the 6000P and 6000C perfecting presses.
Discussing press speeds, Mansfield explains, “When printing on silk or coated papers, the Prosper 6000 series presses can run at 300m per minute. But it’s not just speed that differentiates these workhorses. Kodak’s water-based nanoparticulate pigment inks cost less than pigment inks for drop-on-demand inkjet presses, so Kodak customers benefit from lower operating costs.”
With Kodak Stream inkjet technology, the drop generation technology inside Prosper 6000 presses creates drops in excess of 400KHz, which means each Prosper printhead produces 480,000 drops per second, states Mansfield. “Compare this to drop-on-demand inkjet – used by other inkjet press manufacturers – that range from 25 to 50KHz. That is why Prosper 6000 presses have the fastest raw printing speed.”
Mansfield says, “We have set our sights on converting the traditional analogue printing process – offset and flexo – to inkjet. To accomplish this, we are driving for faster production, better quality and lower total cost of production. Faster production lowers the cost of manufacturing, which in turn improves the profitability of digital print service providers. Better quality enables a wider application range, which increases the revenue and profit for digital print service providers and the technology vendors who serve them. Cheaper total cost of production speeds up the migration of print work from incumbent processes, offset or flexo, to digital. It also improves the profitability of digital print service providers.”
For a heatset web press shop, investing in an inkjet press, like one of the Kodak Prosper 6000 models, may allow them to migrate work from their web press for short run, segmented or even personalised work. This often results in cost savings by reducing paper waste, slashing production time and eliminating plates, he states. They can also capitalise on revenue growth through new sales opportunities.
Says Mansfield: “If the print service provider owns an older model drop on demand (DoD) inket press, a new Prosper 6000 can help them increase their application range beyond the capabilities of DoD presses. This is often seen by moving from low-to-mid ink coverage jobs on uncoated papers to mid-to-high ink coverage jobs on coated and glossy papers. This often results in revenue growth through new sales opportunities and/or cost savings for higher coverage work.”
He says the Prosper range works effectively in catalogue printing, commercial, direct mail, labels, packaging, book, newspaper and magazine publishing, and transactional and transpromo applications.
Océ Australia’s Colin McKenzie says the Océ ProStream 1000 is the next generation imaging technology utilising ever-reliable piezo drop-on-demand 1200dpi print heads.
“With the Océ Multi-level dot modulation (variable droplets likened to offset stochastic screening) the FOGRA 51 print quality standard is achieved, in combination with Océ’s latest, newly developed polymer pigment ink set.
“What the commercial printer can look forward to is the consistent print quality related to customer branding on offset coated stocks, reliability and minimal operator intervention.
“Like all digital webfed presses the inline finishing options are available in abundance,” he notes.
As run lengths reduce, EFI says its Nozomi C18000 is a cost effective solution to today’s customer demands for ever-reducing response times, versioning and variable data, just-in-time and on-demand printing – all of it designed to cut inventory costs and waste.
The Nozomi offers high-quality, high-speed digital LED printing up to 75 linear metres per minute (with one- and two-lane printing) on stocks up to 1.8m wide.
Designed with continuous operational, environmental, and competitive improvements in mind for innovative print providers, the Nozomi delivers resolutions up to 360×720 dots per inch, and single-pass, LED, digital drop-on-demand piezo inkjet technology with four-level greyscale imaging.
Combined with this is a variety of configurations including CMYK, CMYK+W, CMYKOV, CMYKOV+W and an inline primer that allows dot gain and ink absorption control over a range of corrugated top sheets.
EFI offers a totally integrated platform with top- and bottom-feed options for a digital corrugated packaging. The press uses a patented system handling media separation, lift, transport and alignment at full press speeds, with programmable features for speedier, automated feeding configurations on repeat work.
The Nozomi digital packaging solution offers compelling advantages in the elimination of waste by printing only what is needed at the time it is needed, making it an ideal fit for market segmentation and time/region-sensitive promotions.
However the trend towards ship/shelf-ready packaging favoured by popular Big Box retailers is where multiple products remain inside the outer corrugated carton from warehouse to shelf, notes EFI. That provides an opportunity to upscale the printing of higher quality, full colour graphics rather than just standard single-colour blocks with heavy text and barcodes on the outer box.
EFI also identifies strong growth in online shopping and in corrugated packaging used by internet retailers such as Amazon to protect goods en-route from automated warehouses to residential addresses.
With variable web widths from 320mm to 520mm, Xeikon’s TrilliumOne is based on liquid toner technology for high speed and quality. It is targeted at printers in direct-mail and catalogue production. Using coated substrates, and with full rotary printing, it harnesses Xeikon’s Trillium liquid toner printing process, which the manufacturer offers as a revolutionary entry into a market targeted by inkjet hardware vendors.
A combined development between Xeikon and Miyakoshi, TrilliumOne blends the expertise of the two high-ranking companies – Miyakoshi’s specialisation in press mechanics and Xeikon’s philosophies in digital imaging, high-speed electronics, high-resolution LED technology, workflow and toner processes.
From HP comes the HP Scitex 17000, which it says delivers higher levels of productivity, makes easy work of high-volume digital post-print production, and prints at 1,000sqm per hour. It easily accommodates warped media, using hands-free operation and an automated feed, with zero setup. The 17000 operates smoothly on industrial-grade corrugated board, with stack-to-stack operation and automatic loading.
An upgrade of the popular 15000, the 17000 uses HP’s HDR technology and prints on coated media using HDR Scitex inks for cost effective corrugated packaging printing. HP sees the 17000 reaping the benefits of digital production for corrugated applications without the usual tradeoffs of slow throughput and waste.
JCI provides imprinting inkjet printheads to integrate inline with presses or mailing equipment, turning conventional equipment into hybrid solutions, performing conventional printing and variable printing in a single pass. More importantly, such hybrid solutions ensure high productivity and lowest running cost for users to be competitive in the market.
JCI adopts DoD piezo inkjet technology from Ricoh and Kyocera, providing the Hawk inkjet system using a Kyocera 108mm printhead at 600×600 dpi, up to 100mpm, and the Sparrow inkjet system using a Ricoh 54mm printhead at 600×600 dpi, up to 100mpm. Both systems are available as UV or water based.
Garry Morrison, sales manager, JCI Applications, says, “Typically mailing houses use low investment cartridges systems paying dearly for running the system in the form of costly ink and cartridges. The Sparrow Inkjet system is a good replacement to the cartridge system since its investment is not high and its printhead will last over two to three years. Its total cost of operation will be much lower compare to the cartridge systems.
“Printers can turn a conventional offset press into a hybrid solution costing only a fraction of more-costly full digital presses, yet are highly productive with their inline production mode.”
Hybrid webfed/sheetfed
Peter Scott, managing director of Screen GP Australia, recalls that when the 520HD press was introduced to the market just over two years ago, print businesses were impressed by its offset-like image quality. “It was the first time high-speed inkjet demonstrated the capability for effectively printing jobs that approached offset quality. Development has been ongoing since that time, with the SC inks being the most significant advancement.”
Drying and curing is a constant issue with high-volume inkjet, says Scott. “There is a lot of water to get rid of and now, with the new Near Infrared (NIR) dryer, we can achieve what no other digital inkjet press does. NIR drying technology dramatically advances productivity for work demanding high image quality and expands print applications for high-speed inkjet across a broad landscape of products.”
The new Screen NIR dryer technology, built into the existing press frame of the 520HD, extends drying performance for both lightweight uncoated stocks and heavier-weight, coated litho substrates. The result is an expanded range of applications and even higher productivity on difficult to dry substrates. Drying on the 520HD is now three-tiered: heat dissipation, hot air assist, and infrared. This integrated solution achieves a drying balance along the entire paper path tuned specifically to the characteristics of the paper, reducing or eliminating the cockling often associated with traditional inkjet ink drying methods.
Operators create substrate profiles with embedded drying protocols at different print resolutions and ink limits, explains Scott. These profiles are managed seamlessly by Screen’s proprietary Equios front-end software, providing intelligent drying balance for each specific stock, which helps achieve the highest quality, best speeds and desired ink coverages.
Scott adds: “All new Screen Truepress Jet 520HD machines may be optionally equipped at the factory with the NIR dryer. Screen branded 520HD units currently in the field can be upgraded with the new dryer at the machine site. It’s a major move forward in making production web inkjet a viable alternative to offset – with all of the benefits of no plates, short runs, variable data, offset stocks and streamlined digital workflow.”
At the top speed of 150m per minute, the 520HD generates around 2,000 A4 pages per minute. It works with a paper range of 40gsm through to 250gsm, and features a wide-gamut ink set rivalling offset.
Scott makes the point that the 520HD can deliver cut sheets by printing web and sheeting/stacking at the end. As a UK printer put it, “Not only is the Truepress highly efficient as a digital printer but that efficiency is amplified further by being a continuous-feed press.”
Wide format inkjet
Matt Ashman, sales manager for Durst ANZ, identifies two avenues of technology – UV DTM and Durst Water Technology. “First is high-speed and extremely high-quality UV DTM. The P5 Platform is based around low ink usage – 5 picolitre inkjet printing for fast high quality printing onto many media without any activator or primer.
“The second is Durst Water Technology, which is aimed at both short-run and high-volume corrugated packaging. The technology is ecologically sound, using ink with 80 per cent water, creating odour-free printing and operation,” he says.
Ashman describes Durst’s WT 250 HS as a hybrid 2.5m wide format printer, with high-quality 1000dpi, reaching speeds of 200sqm per hour, while its SPC WT 130 offers extremely high speeds at a standard 1.3m width, 6,000sqm per hour.
Ashman says, “Both deliver wide gamut and smooth solids at those production speeds.”
Ashman says the P5 gives POP and wide format print shops various options – it can be used for the increased demands of super high-quality inkjet printing, but can also deliver capacity and turnaround times when needed in an efficient hybrid machine.
“Meanwhile, the Durst Water Technology gives packaging and corrugated printers the digital versatility they have been looking for, enabling short-run, cost effective and ecologically sound production. That is something that has been a wish of such businesses for some years,” says Ashman.
Ashman sees profitability with Durst through the efficient and reliable workflow, quick media turnaround commercial ink pricing, as well as reliability day in day out.
He says, “A press has to deliver speed and quality, but efficiency and reliability can be an elusive commodity with emerging technology.
“Customers who invest in Durst see these benefits from day one. With the support of local technicians and parts, we provide a professional solution for serious business to profit from.”
Comment below to have your say on this story.
If you have a news story or tip-off, get in touch at editorial@sprinter.com.au.
Sign up to the Sprinter newsletter