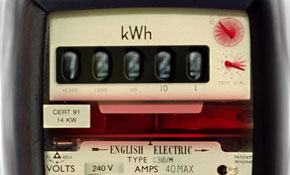
The knock-on effect of oil price rises is to focus printers’ attention sharply on energy efficiency. Some are promoting their efforts under a green flag: energy-efficient manufacturing uses less of the earth’s precious natural resources. But, in the past six years, the unit price of a kilowatt/hour has trebled – and the predictions are for a further 25% increase over the next 18 months. Energy efficiency isn’t just good for the environment – it’s also good for the bottom line.
Take Taylor Bloxham, for instance. Seven years ago, the Leicester-based commercial printer began an investment drive that saw the replacement of four smaller-capacity presses with three B1 machines: two 12-colours with inline reel-sheeters and a six-colour with coater. Capacity has doubled, but the company is using less electricity. This is thanks to the installation of a PowerPerfector voltage optimisation unit and the implementation of a power factor correction scheme (see box-out).
Management systems officer Elizabeth Ashford says that, by 2011, Taylor Bloxham will have avoided putting more than 13 tonnes of carbon into the atmosphere – and saved 25% on its energy bills to boot.
The amount of energy we use was already a priority for us because so many of our customers are now concerned about environmental issues in their print, explains Ashford. But, coupled with the rise in energy prices, it pushed us in the direction of significant measures.
Another PowerPerfector user is magazine printer Buxton Press. Its programme of green measures was driven by chairman Bernard Galloway’s interest in the environment. The voltage optimiser has cut down Buxton’s electricity draw by about 13%, says Galloway. The printer also took a long hard look at the number of compressors on its factory floor, eventually replacing 56 individual units with just three large ones to achieve a massively improved efficiency. All in all, the company spent around £360,000, which it expects to reclaim in reduced energy bills, sooner rather than later, especially when you look at how the cost of electricity is going up, adds Galloway.
Benefits of scale
Electricity use is naturally always proportionate to a company’s turnover. As a result, some of the UK’s largest printers have been prompted to harness their scale of operation to drive improvements in energy consumption. Prinovis’ state-of-the-art gravure factory in Speke, Merseyside, uses its own combined heat and power (CHP) facility which, via two five-megawatt turbines powered by natural gas, generates enough power to run the plant’s gravure presses, drive its closed-loop solvent recovery system and power the chillers that refrigerate the press units and run the factory-wide air-conditioning system. Heat from the presses is also recycled using CHP technology and transmuted into electricity to power the Prinovis office and administration facilities. Prinovis sales director Ross Borton says the Speke site is following in the footsteps of Prinovis’s Nuremberg facility, which has been using CHP technology for a decade.
The CHP principles have several great attractions for us, explains Borton. There’s the environmental angle, which is very important to our customers and core to Prinovis’s principles; the cost-savings, which are increasingly important as energy prices increase; and finally the fact we’re self-sufficient for energy.
These printers have all made significant investment to reduce their energy consumption, but there is a lower-outlay option. In fact, there’s a guaranteed payback to one approach in particular: the Energy Maps process invented and implemented by energy consultant Enigin.
Enigin regional director Steve Hayden explains: Energy Maps is a four-stage process that takes up to 12 months to implement. It begins with an energy audit and monitoring devices are installed that show your consumption. After monitoring, we install some of the most effective devices on the planet for saving energy.
Based on the results of the initial audit, Enigin writes a guaranteed saving on its Energy Maps programme of up to 40% and Hayden promises that if we don’t deliver that saving, we refund the difference. On top of that, the Carbon Trust runs an energy-savings loan scheme, which funds the Energy Maps programme on an interest-free basis. So, each month, the printer pays back the Carbon Trust less than their current electricity costs. And the more electricity prices go up, the quicker they reach return-on-investment.
Enigin, despite being new to the print industry, is currently working with around a dozen printers, from the small-scale (Southampton’s Indigo Press is currently moving out of the monitoring stage and into implementation) to the huge (Newsquest’s Oxford plant, which was spending £280,000 a year on its electricity, but thanks to the Energy Maps programme is now saving around 30% annually). The programme works for all sizes of printer, but the best returns are generated by those who have an electricity spend of more than £20,000 a year, says Hayden.
Increased profitability
Even the monitoring stage of the Energy Maps programme can produce startling results. Enigin monitored a small print company in the south-west with two identical European-built presses, one just a year older than the other. We established that one of the presses was using 40% more electricity than the other. That’s allowed the printer to prioritise machines in relation to the cost of the job and they’re already adding to their profitability because of it, says Hayden.
One key factor in improving energy efficiency is in employee education – and it’s often the most overlooked. Hayden says: People are the biggest wasters of electricity, and educating them is crucial to the success of any improvement programme. Enigin offers what Hayden calls powerful motivational collateral to its clients, including screen savers, posters, mobile and computer wallpapers and an incentivisation programme for employees’ energy-reduction ideas.
Taylor Bloxham’s Ashford also thinks employees are a major factor: We’ve put a lot of time into educating our employees, because there are lots of things that can only generate energy savings if people understand what to do and why they’re doing it. It’s really important to spread that message. Otherwise, staff go home leaving lights on and photocopiers on standby and it soon mounts up.
There isn’t a printer in the UK who needs it spelling out, but Hayden does anyway: Printers can’t afford to spend money on wasted electricity – there simply isn’t the profit margin in the industry to allow for that. And the irony is that every single UK business is paying the Climate Change Levy, which all goes straight into the Carbon Trust’s loan scheme. They’re funding other companies to take up energy-efficient technology. Jump on the bandwagon – you can only win.
TECHNOLOGY: ENERGY EFFICIENCY
Power factor correction (PFC): Power factor is a measure of how efficiently electrical power is consumed. 100% efficiency (a power factor of one, also known as ‘unity’) is the ideal; anything less than one means extra power is required to do the job. This extra power is called reactive power and represents an extra burden on the electricity supply. Power factor correction restores the power factor to as close to unity as possible. Find a PFC primer at www.enspecpower.com
Voltage optimisation: The UK’s electricity supply is set to ‘over-voltage’, which means that single- and three-phase electricity is typically supplied at around 240v. Most equipment uses only 220v and the over-voltage can drive motors, for instance, into ‘saturation’, which wastes energy as heat. A voltage optimisation unit monitors and adjusts the incoming voltage at a site, thereby cutting electricity draw by up to 15%. The PowerPerfector voltage optimiser claims carbon emission reductions of up to 22%. More information from www.powerperfector.com
Combined heat and power (CHP): This is a technology that generates usable heat and power in a single process. At its simplest, it begins with a turbine or an engine to drive an alternator to produce electricity that can be used on-site. The heat produced during this generating process is recovered in a heat-recovery boiler and raises steam, which is then used as power. CHP is rated as a highly efficient way to use both fossil fuels and renewable energy. Visit the Combined Heat & Power Association www.chpa.co.uk
Read the original article at www.printweek.com.
Comment below to have your say on this story.
If you have a news story or tip-off, get in touch at editorial@sprinter.com.au.
Sign up to the Sprinter newsletter