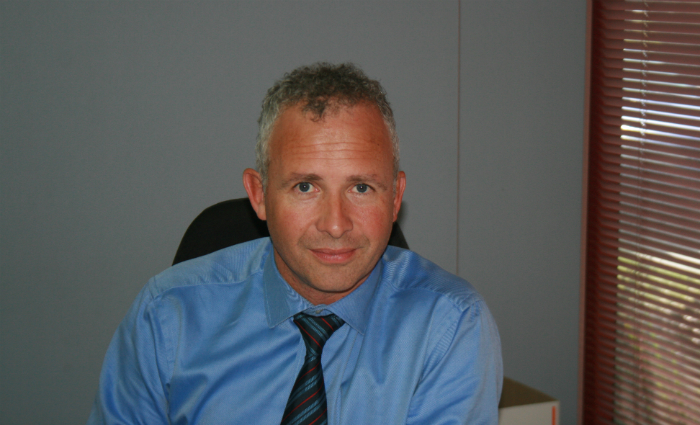
ColorPak has shed more jobs in its third plant merger in as many years but expects costs savings to make up for dipping sales and higher debt in the next financial year.
The 90-year-old carton printing giant, which just released its half-yearly report, is also investing about $6m in new equipment, including a HP Indigo WS6600 digital press, Roland 700 six-colour offset press, additional paper cup forming machine, and new Esko machine to double capacity in flexographic plate-making for design and prepress component subsidiary Brandpack.
The digital press marks ColorPak’s first foray into digital printing
The company expects $3m savings in FY2015 from the Mt Waverly, VIC plant closure and all job losses are through voluntary redundancies accepted before Christmas last year.
It has just reported an FY2014 half year normalised net profit after tax down $2m from the same period last year of $2.7m, excluding the $2.4m one-off restructuring costs. The plant merger and new equipment is expected to double the capacity of the Braeside, VIC site.
[Related: More packaging news]
Sales fell about $20m from 2012’s $190m, which increased almost $70m from 2011 as Carter Holt Harvey Cartons (CHH) was bought out, cashflow decreased, and debt increased from $32.995m to $35.288m, but EBITDA came in at $7.4m with the margin down from 11.5 per cent to 8.9 per cent.
Managing director Alex Commins blamed lower sales on Cadbury’s decision to switch from cardboard packaging to flexible flow wrap, losing ColorPak $5m, and sluggish volumes and lower prices from other clients.
The report says the series of plant mergers are to reduce duplicate labour cost, downsize occupancy footprints, and use scale as leverage for improved input cost purchasing following its acquisition of CHH in 2011.
Commins says the company has reduced its staff from about 820 to 650 following the acquisition through redundancies and natural attrition.
He says original plants in NSW and Victoria were combined with CCH plants and relocated to bigger sites nearby to accommodate new equipment, but the company will keep the plant it acquired in Auckland, New Zealand.
“The last six months have been challenging for us, it’s no easy feat to integrate two large companies,” he says.
“We are building a strong platform for future growth and will continue to invest in equipment to underpin this aspiration.”
Despite the expenses, the company returned the same level of dividend to shareholders and expects revenue to return to normal levels in the future and improve with better market outlook thanks to a lower Australian dollar and rising consumer confidence.
“To have any growth in such upheaval is very challenging,” Commins says.
Comment below to have your say on this story.
If you have a news story or tip-off, get in touch at editorial@sprinter.com.au.
Sign up to the Sprinter newsletter