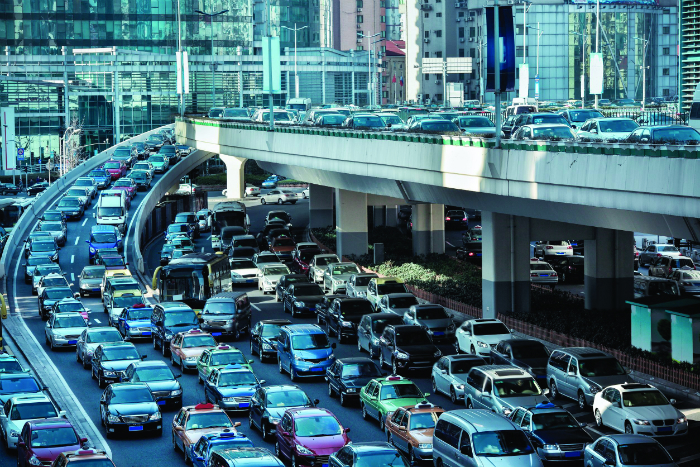
Eliminating the bottleneck between slow-moving plate production and speedy presses is a step towards greater productivity.
Meanwhile, plates have come a long way – sharper dots, greater durability and more flexibility with specialty paper stocks. And all of it comes wrapped in a cleaner, greener package nowadays, with chemistry-free and processless plates becoming common, and even those plates that use chemistry are not using the toxic stuff that was still commonplace a decade ago.
Productive plate setters
Productivity in prepress comes to the fore with Heidelberg’s Suprasetter plate setter, says Dierk Wissmann, HANZ’s CTP and workflow product manager, starting with its plug-and-play functionality – the Suprasetter arrives pre-installed and ready to use. The laser head, designed by Heidelberg engineers, is built for long life and comes with a seven-year warranty. There is inbuilt temperature control to ensure a stable environment, which makes Suprasetter popular in rural locations and tropical climates.
Suprasetter has low energy consumption, meeting environmental concerns and reducing operational costs. Every Suprasetter is delivered with a CO2-neutral certificate confirming that Heidelberg has offset the carbon used in manufacture of the unit, says Wissmann. The machines are field-upgradable and feature unattended operation.
“They require minimum maintenance, as the units self-check each day when they are turned on. For the rare occasions when there is a problem, Heidelberg’s engineers can remotely access the machine to make a diagnosis, ensuring minimum downtime,” he says.
The popular Suprasetter A75, for the A2/B2 market, comes in various configurations, including Automatic Top Loader and Dual Top Loader for high volumes. It produces plates at 2540dpi up to 5080dpi for special applications such as stamps and security printing. “The A75 runs on low power consumption,” emphasises Wissman, “using only five watts on standby and 550 watts on average when imaging.”
Screen has introduced its new PlateRite PT-R4600 4-up plate setter with fibre LEDs for sharper, higher-definition plate imaging. A speedier Z model is capable of 33 plates per hour at 2400dpi. Screen Australia’s managing director Peter Scott sees the new setters as more environmentally friendly in terms of power consumption. In Eco mode, power consumption is reduced by between 74-83 per cent while idling. Main power supply is down from 20Amps/4.0kW to 15Amps/3.6kW but despite this, the laser power is up 13 per cent, ‘making the PT-R4600 ideal for low-sensitivity processless plates such as Fujifilm Brillia Pro-T and Agfa Azura TS/TU,’ says Scott.
Three models comprise the PT-R4600 series, designated E, S and Z. Productivity is 11, 21 and 33 plates per hour respectively. Another saving for B2 printers is that the optional ‘bridge’ to connect the CTP setter to a processor is now built-in.
Steve Peck, project and marketing manager, graphic systems at Fujifilm, says the vendor offers two lines of CTP systems: the compact A1 and B2 Suprasetters from Heidelberg, and the PlateRite PTR systems manufactured by Screen. Fujifilm XMF workflows power all of its output devices and is designed to meet the production demands of sheetfed, web and digital printing, bringing together Fujifilm’s expertise in colour, imposition and workflow production.
“Companies are able to run CTP equipment over multiple shifts to allow more production output and CTP devices are still developing and becoming faster and faster,” he says.
Thermal CTP is the cleaner, more environmentally friendly route, says Currie managing director Bernie Robinson, and the Cron-ECRM range of drum setters from China is Currie’s solution in this market. Cron and US-based ECRM formed a joint venture in 2014 and began selling devices the following year. Currie has been selling Cron plate setters since 2010, with eight sold last year and a similar number in 2014, as the brand grows in popularity.
The 26 and 36-series are available, with a 56-series soon for release. The thermal CTP units range in size from two-page-up to VLF, with a choice of lasers. Each model can accommodate any print job from A4 to A1, with ample space for register and trim marks, as well as colour bars. The latest-generation lasers, together with patented plate handling technology, ensure maximum reliability with fast throughput. With up to 56 plates per hour, TP3696 models can keep several different format presses fed with work, optimising press utilisation, flexibility and overall productivity.
Each model in the range has laser options designed to match budget requirements. F and G models have different laser architectures, with G models having the latest generation, liquid-cooled technology. Optional plate feeders, punches and handling systems are available to further tune installations to production needs, automating and streamlining workflow. The processor has a choice of a washout unit or plates can be washed on-press.
Cron setters can be configured for manual loading, but in the interests of productivity, can be fitted with automatic loaders – the 50N3 (three cassettes for three differently sized plates) and the 50N5 (five cassettes for five differently sized plates). The CTP unit, with auto plate loader and stacker comprises a turnkey prepress solution with little manual handling, says Robinson. The CTP line is compatible with a wide range of front-ends, but Currie can supply Founder or ECRM RipMate software in its WorkMates workflow.
Robinson emphasises that in Australian A2/A1 commercial printing, there is generally not the need for extremely high plates-per-hour ratios, as jobs going on eight or ten-colour presses tend to be anywhere up to around 50,000 impressions. Nonetheless the Cron setters can produce up to 90 plates an hour (and down to 15 an hour), depending on the number of lasers.
Agfa Oceania managing director Mark Brindley details Agfa’s thermal and violet setter range – the thermal Avalons N4, N8 (B1-size) and N16 (VLF), and the violet Advantage N for conventional and chemistry-free commercial and newspaper applications.
“Azura CX85 and CX125 clean-out units are showpieces of Agfa’s expertise,” says Brindley. “Their cascading clean-out technology enables you to handle more plates, with lower waste costs. The pH-neutral water-based gum circulates between two shallow trays, which raises the clean-out efficiency and reduces gum consumption. It also lengthens the bath life.
“Choose your model: connected online with the plate setter, or standalone. There is no need for a developer or replenisher and everything is preset. So once the Azura CX85 or CX125 is installed, you’re good to go — the unit is designed to handle some 40,000sq m of plates a year.”
Anthony Harvey, Kodak Australasia’s marketing director, points to its platesetter line-up: Achieve, Trendsetter and Magnus, covering the needs of smaller printers with affordable manual CTP to some of the largest printers with fully automated CTP solutions, even with large format automatic pallet load systems to maximise operational efficiency.
He says Kodak is using two light valve based imaging technologies: TH5 imaging technology used in Achieve plate setters and Squarespot imaging technology used in Trendsetter and Magnus plate setters. The recently introduced TH5 imaging technology is based on Kodak’s 20 years’ experience of designing and building light valve based thermal imaging heads, while Squarespot imaging technology, introduced at drupa 1995, is still market leading technology in quality and stability.
In a prepress operation where the plate volume continues to increase, driven by shorter run length jobs, the need to have a flexible and efficient prepress operation becomes even more critical than before. This is when prepress automation becomes essential – from the Kodak Prinergy Workflow software which manages incoming files to the additional CTP automation options, allowing you to have a large range of plates (including plates for multiple presses online in the CTP) that can be imaged automatically without direct operator interaction to the equipment.
“Kodak is also investing in new options to connect remotely to your CTP using a mobile application from your handheld device. This will enable printers to easily attend to their operations remotely,” says Harvey.
Right plate for the right job
Heidelberg is marketing its Suprasetter family with Fujifilm’s ZAC plates range, which it describes as ‘low on chemistry and maintenance’. The ZAC LH-PJE and LH-PLE plates use Fujifilm’s ZAC processing system to minimise use of chemistry and water, allowing print businesses to meet their environmental expectations, as well as reducing maintenance, explains Kevin Birch, HAN’s consumables manager.
“The Fujifilm ZAC system provides optimised processing quality by using intelligent developer replenishment. This results in a significant reduction in the volume of chemistry and water used, which helps you to reduce your environmental footprint. The ZAC processor can achieve up to an 80 per cent reduction in chemistry by identifying only the areas on the plate that actually need processing and by constantly measuring the bath conductivity. The intelligence of the ZAC system means there’s hardly any need for operator intervention. In fact, once installed, the whole system looks after itself. Plates are produced consistently, without effort, and quality is maintained.”
Birch says the ZAC/Fujifilm plate combination is ‘the closest to processless chemistry reduction with the benefit of a processed plate’.
Maintenance requirements are also slashed, thanks to the intelligent replenishment system that monitors the developing conditions and accurately calculates the required volume of replenisher. Bath life can be extended up to four months or 15,000sq m, maintaining the highest quality dot structure and stability. “This means maintenance is reduced to less than half the time of many other processors and may only need to be carried out four times a year,” adds Birch. “This is a massive saving in labour and wasted time for businesses that are trying to achieve more with less staff.”
In addition to the ZAC system, Heidelberg also offers the complete range of Fujifilm’s new Superia thermal and violet CTP plate technologies that includes the LP-NV2 processed plate technology, the Pro-V low-chemistry option (which uses only a finishing solution instead of the traditional developer or replenisher for violet systems) and the Fujifilm processless thermal PRO-T3, which eliminates the processor, chemistry, gum and water used in the conventional plate production process.
Fujifilm’s Steve Peck says its Superia low-chemistry range covers thermal and violet plates. Superia LH-PLE is a positive thermal plate for longer commercial runs, while Superia LH-PJE shares those characteristics and is designed for medium runs. And Superia Pro-V is a violet plate for medium to long-run commercial work. Superia ZP offers true processless CTP that eliminates the processor, chemistry, gum and water, with the plate being taken straight from the plate setter onto the press.
The lo-chem range from Fujifilm “significantly reduces chemistry consumption and maintenance through unique intelligent monitoring and replenishment”, says Peck. More commonly used run lengths generally use Superia LH-PJE and PLE which exhibit sharp dot characteristics from 1-99 per cent, suitability for FM screening down to 10 microns, as well as being suitable for UV inks. Superia ZP processless plates suit FM screening down to 20 microns and shorter run lengths under 100,000, and also hold a sharp dot from 1-99 per cent.
Looking ahead to this year’s drupa, Agfa’s Mark Brindley says the company will introduce a new chemistry-free plate, the N95VCF, ‘which will push chemistry-free technology to a new level. This new plate will give newspaper printers large or small greater flexibility to take on any job’. Its improved robustness on-press will support run lengths of up to 300,000 impressions in high resolution, support UV printing, and offer high image contrast plates, making plate inspection and optical recognition by punch bending equipment easy, and avoiding mix-ups on press. Once cleaned-out, the plate is fully daylight resistant and offers high scratch resistance.
Currie’s Bernie Robinson says that for environmental friendliness, speed and ease of use, chemistry-free plates are making rapid inroads on chemical plates that require developer to image the plates, and they now share the commercial market half-and-half.
Elimination of chemical process variables (developer, replenisher and rinse-water) reduces waste and the disposal costs associated with it. Moreover, elimination of process variables provides reliable, consistent and high-quality results. Currie supplies Agfa’s Azura thermal chemistry-free plates (TE plates for up to 75,000 impressions and TU plates for up to 150,000 impressions), which require only gum washout, either from a washout unit or on-press. Violet plates are still popular as a lower-cost entry point into CTP, in terms of buying and maintenance (there is only one laser and it tends to have a longer life than the multiple lasers in thermal). Currie Group offers Agfa’s chemistry-free violet Azura VI plates. Violet is still a force, not so much the old silver plates but Currie Group runs a sizeable trade in second-hand ECRM-Mako violet photopolymer plate setters. However, Robinson emphasises that for the chemistry-averse printer, while violet offers a product in that chemistry-free market, thermal is the “cleaner” alternative.
Kodak’s Anthony Harvey says the company recently launched a range of new plates – Electra Max thermal plates provide maximum chemical resistance on-press, including on UV and H-UV presses, and “maximum” unbaked run lengths, print resolution capabilities, and chemistry savings. Libra V digital plates come in two varieties – for newspaper production and commercial work.
Meanwhile, Kodak reports some 3,000 customers worldwide for its process-free Sonora XP plates, aimed at commercial, publishing and packaging printers and its Sonora News process-free plates for newspaper printers. The Sonora plates completely eliminate processing equipment and chemistry, along with all the costs and environmental impact of the processing or clean-out step.
“Sonora plates go straight from the plate setter to the press, with no intermediary processing or clean-out step,” notes Harvey. “Therefore, all of the environmental impact of the processing step is completely eliminated, including: water, chemistry (production, shipping, worker exposure, and disposal), processing equipment (production, shipping and eventual disposal), and energy usage.”
WRH Global Australia (formerly Ferag Australia), which partners with Screen Australia, distributes both thermal and violet plate technology. The Xingraphics Primus Plus conventional thermal plate offers the twin benefits of low water usage – and this also equates to lower ink usage due to its shallow coating. The Eco-V and Million plates from IBF are its violet offering, says WRH Global’s general manager Ian Martin. Meanwhile, developer IBF has just released the Eco-T plate which can be used as both a chemistry-free/neutral pH wash-out plate or a DOP (Develop-On-Press) plate.
“The Xingraphics Primus Plus plate offers water savings in excess of 25 per cent, in comparison to many competitive plates, and ink savings ranging from five-15 per cent,” explains Martin. “The ECO-T from IBF utilises a pH-neutral wash-out solution which has a long bath life and can also be used directly on the press as a DOP plate."
Comment below to have your say on this story.
If you have a news story or tip-off, get in touch at editorial@sprinter.com.au.
Sign up to the Sprinter newsletter