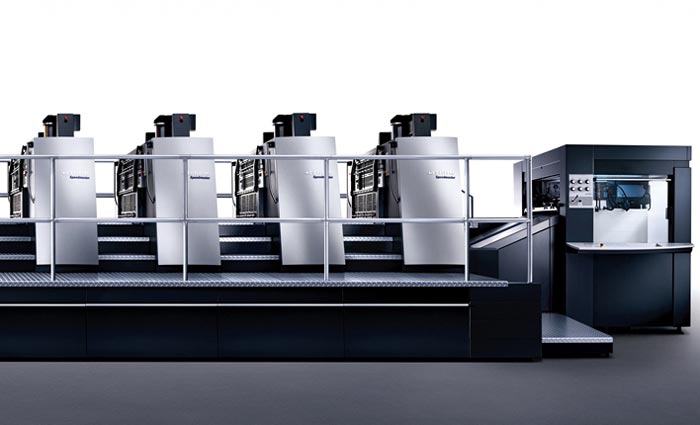
When Heidelberg unveiled the Speedmaster XL 105 at Drupa 2004, the German manufacturer had high hopes for the new press, which it claimed could replace two similar SM 102s or competitor machines. Two years later, a full UV version and dual coating variant were unveiled. At Drupa 2008, an eagerly awaited perfecting version – the XL 105-P – was launched. This new machine was capable of handling sheets of up to 730×1,050mm running at a maximum speed of 15,000 sheets per hour (sph) in perfecting mode. It immediately found favour with high-volume commercial printers.
It’s little wonder that the launch was so successful when you consider that Heidelberg claimed this super quick press had the potential to produce up to 60 million sheets per year even when it was fitted with the most basic specifications.
That was four years ago. Since then, the industry has undergone a phenomenal transformation. It is partly in response to these changes that Heidelberg unveiled a new version of the XL 105-P in December.
With a top perfecting speed of 18,000sph, the new machine offers a significant speed hike over its predecessor and is the next step in the evolution of the XL range of presses, explains Heidelberg general manager of product management Lindsay Barnes.
“In today’s aggressive market, print shops need to move jobs in and out as fast as possible to remain competitive. Whether doing short runs or long, it’s about output,” says Barnes. “The faster a printer can complete his work, the lower the cost per sheet becomes.”
However, the impressive speed increase isn’t the only new addition to the XL 105’s specifications. “Both the XL 105 and XL 75 have a host of unique features, from the automatically adjusted transfers cylinders, venture guide plate system, dynamic sheet brakes and suction disc delivery, which make the XL a true ‘18k’ machine,” adds Barnes.
Drum roll please
When running at high speeds, a modified storage drum and improved reversing drum with new pincer gripper system increase the retaining force and ensure precise registration, claims Heidelberg. At the delivery end, there’s also the new CleanStar, which “supports more efficient powder extraction and minimises powder levels around the press,” says the vendor.
As demonstrated at an open house at Heidelberg’s Melbourne Print Media Academy last October, the XL 105 also boasts simultaneous plate change, which allows press operators to get the next job ready in the time it would normally take to change one plate on a printing unit.
It also showed off Prinect Inpress Control for inline colour control on the fly. This spectrophotometric inline measuring system is integrated into the press and is capable of measuring process colours, spot colours and register in the print control strip. If any corrections are required, these are forwarded directly to the Prinect Press Centre where they can be adjusted without affecting productivity.
Although the machine is set for a global launch at Drupa 2012, two XL 105-P presses have already been installed at beta sites with customers who are working closely with Heidelberg’s head office in Germany. To date feedback on the machine’s production capabilities has been excellent, according to Barnes, who claims that the press consistently per-forms at its top rated speed of 18,000sph.
The first beta XL 105-P was delivered to UK-based Sterling Press last year. The printing company is a longstanding Heidelberg customer. It installed the world’s first XL 105 10-colour perfecting press with Heidelberg’s reel-to-sheet module, CutStar, in 2008, and has increased productivity by 20% since taking delivery of the new XL 105 beta, according to co-owner John Pizzey
“We tested short-grain versus long-grain because most of our work is short-grain through the CutStar, so performance on that was very important,” Pizzey told ProPrint’s UK-sister title, PrintWeek, in November. “We are running flat out and nearly every job is running at 18,000sph. Even with jobs on trickier stocks that would have run at 12,000sph on the older presses, we are able to run at 16,000-17,000sph on the new perfector.”
The Sterling Press configuration includes a CutStar roll sheeter. While these are fairly commonplace in the UK, Barnes says that take-up by ANZ customers isn’t as strong largely because, unlike in Australia, “in the past there was a substantial cost difference in the UK between reel stock and sheeted stock which made it easier to justify the purchase of CutStar devices”.
He doesn’t expect to see a rash of CutStar orders any time soon from ANZ printers. But based on the manufacturer’s expectations for the new machine, do expect to start hearing about local XL 105-P installations after the press debuts at Drupa in May. Global shipping com-mences after the show ends and Barnes says that Heidelberg hopes to sell 200 presses in the first year. He concedes that the company would be “pleased with one or two given the state of the economy”.
First impressions
Many of these installs are expected to be from customers looking to replace existing Heidelberg machines but Barnes refuses to be drawn on how much interest they’ve had in the new machine so far.
“It’s too early to comment apart from restating that we already have a substantial installed base of SM 102s and would consider these customers to provide a solid prospect base,” he explains. “Many companies are looking to rationalise their existing fleet of presses by investing in the XL platform to allow them to reduce their equipment and associated costs.”
While Australia is already home to four XL 105 long perfectors, including the high-spec machine installed at McPhersons Printing last March, chances are that there will be plenty of businesses interested in the new machine.
As you’d expect from an operator like Heidelberg, there’s a variety of different service packages on offer to entice prospective buyers, ranging from complete coverage for parts and labour to tailor-made service contracts. Availability of spares is rarely an issue, according to Barnes, with many of the components of Heidelberg press used across the full range, which allows the business to achieve a supply rate of more than 90%.
“Because of our large market share and impressive installed base of XL presses, we already have an established after-sales support infrastructure with parts holdings in each state as well as major warehouses in Sydney, Melbourne and Auckland and direct links to the world logistic centres in Hong Kong and Germany,” he explains.
As for the price of the new press, Barnes refuses to be drawn on details because “it’s not about the cost, it’s about the ROI”. With this high-volume machine, that’s exactly what Heidelberg is promising its customers.
The productivity levels of the manufac-turer’s XL range is unquestionable. Barnes claims that one XL user in the US achieved an annual output of more than 100 million sheets in their second year of production, with many other printers consistently achieving more than 60 million impressions per annum. This is why there are thousands of XL installs globally.
Critical reaction
But the big issue facing Heidelberg in the coming months isn’t going to be convincing potential customers about the quality and productivity levels of the XL 105. It’s persuading them that it makes sense to invest in a lean, mean printing machine in this modern era of falling volumes and overcapacity.
Barnes for one is in little doubt that the numbers stack up. “Faster output speeds are not just for long-run printers,” he argues. “Print shops doing runs as low as 10,000 can achieve significant cost savings with higher output speeds. Take a printer doing seven jobs of 10,000 runs per shift. By increasing his output speed by 20% over the shift, they can save 10 minutes a job, over a shift 70 minutes and over a week 840 minutes a week. That’s 14 hours a week in time saved on production.”
It’s a compelling argument and one that might just work in the current climate that sees all printers striving to become lean manufacturers.
Specifications
Max sheet size: 750×1,050mm
Paper thickness: 0.03–0.60mm
Max speed: 18,000sph (perfecting mode)
Contact: Australia: 1300 135 135; NZ: 0800 803 865, www.au.heidelberg.com
The alternatives
KBA Rapida 106
The Rapida 106 boasts a maximum production speed of 18,000sph straight printing and 15,000sph in perfecting mode. It is equipped with KBA’s DriveTronic Simultaneous Platechanging System (SPC) and also features quality assurance software QualiTronic, DensiTronic and LogoTronic to ensure every page is right, every time.
Max sheet size: 740x1060mm
Max speed: 15,000sph (perfecting mode)
Contact: KBA Australasia 0419 616427 davelewis@kbaaustralasia.com.au
Komori Lithrone SX40RP
Based on Komori’s flagship Lithrone range, the SX40RP, which is a one-pass two-sided printing press, boasts a wide range of state-of-the-art features, including Asynchronous Automatic Plate Changing System (A-APC) for short makeready times.
Max sheet size: 750×1,050mm
Max speed: manufacturer says this varies depending on specification
Contact: Ferrostaal (02) 9338 3900 gerard.wintle@ferrostaal.com
Manroland R900
The R900 enables up to 64 A4 pages to be printed on one sheet. It has a top speed of 12,000sph (format 7B) and 11,000sph (format 8) in straight printing mode with a maximum speed of 10,000sph in perfecting mode. Capable of printing on sheets up to 1,310×1,870mm the XXL perfecting press (in format 8) can handle a sheet that’s 10mm longer and 20mm wider than a straight perfecting press of the same format, claims Manroland.
Max sheet size: 1,310×1,870mm
Max speed: 10,000sph (perfecting mode)
Contact: Manroland Australasia (02) 9645 7900 www.manroland.com.au
Comment below to have your say on this story.
If you have a news story or tip-off, get in touch at editorial@sprinter.com.au.
Sign up to the Sprinter newsletter