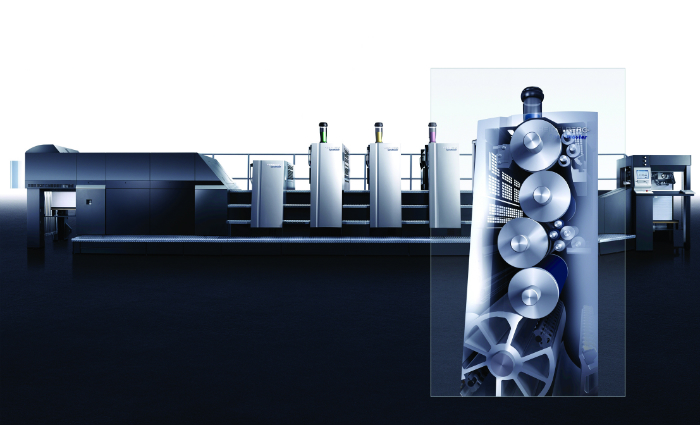
At drupa 2012 Heidelberg gave its new B2 sheetfed Speedmaster XL 75 Anicolor pride of place in the cavernous halls of the Messe. The five colour machine with coater was billed as a totally unique piece of kit by the German manufacturer, with Heidelberg’s then chairman and chief executive Bernhard Schreier declaring that the company had hit upon a revolutionary new formula for the printing industry – “90:50:50” (more of which later).
With Heidelberg racking up more than 1,000 sales of its B3 format Speedmaster 52 Anicolor predecessor it’s clear that it had high hopes for the new machine, which entered series production earlier this year, and is now available to order in Australia, after extensive beta testing at undisclosed sites in mainland Europe.
The thinking behind the launch of a B2 version was relatively straight forward, according to Richard Timson, managing director of Heidelberg Australia and New Zealand. “The demand for shorter runs in both commercial B2 format signatures, as well as packaging for proof runs and boutique short run packaging products, represents a growing market opportunity for printers who avail themselves of the lower waste sheets, faster makeready and higher consistency that they can achieve with the XL 75 Anicolor,” says Timson.
Target market
Initially the machine has only been made available in straight configurations and is targeted predominantly at packaging printers – some of the original beta sites were packaging companies – although perfecting versions are expected to begin shipping later this year along with an eagerly-awaited UV option.
The XL 75 Anicolor has been particularly positioned to help packaging printers take advantage of the current drive towards short run packaging. With packaging printers expected to deliver the twin demands of absolute colour consistency and a variation of coating effects, the combination of the anilox inking and coating unit on the XL 75 Anicolor means that users are “guaranteed” to meet these expectations, says Timson.
“There is minimum colour variation as the anilox system applies a metered exact amount of ink on every revolution,” he explains. “The coating unit also offers various possibilities for coatings, which is a demand for the packaging segment. Many printers also wish to produce sample runs for larger clients – sometimes up to 1,000 copies. They need an exact offset reproduction that cannot be achieved with digital presses. With the size of the press in F format 60x75cm, low makeready waste sheets and speed of the makeready – approximately five minutes for a 6+L – this is easily achieved with the XL 75 Anicolor.”
Packaging isn’t the only target market of course. Heidelberg believes that the XL 75 Anicolor will also appeal to commercial printers who are increasingly handling shorter run lengths and whose costs are constantly being put under pressure. To this end, Heidelberg claims that the machine offers a 90% reduction in makeready sheets compared to a standard offset press, which immediately helps to improve a printer’s profitability.
“With production speeds of up to 15,000sph we can also effectively address longer runs as there is no click charge,” says Timson. “This segment also requires substrate flexibility for brochures, inserts and folders with a stock range of 0.04-0.8mm – the XL 75 Anicolor offers maximum flexibility.”
The last, but by no means least, target market is web-to-print. As Timson explains: “In this market segment it is all about printed sheets on the floor. The XL 75 Anicolor helps printers do just that thanks to its speed and reduced makeready times, as well as the coating effects and format size. Gang printing jobs with various inking levels can also easily be handled.”
Technology
The XL 75 Anicolor is the “next step” in Heidelberg’s development of the Anicolor technology that it initially premiered at Ipex 2006. This was subsequently introduced to the SX/SM 52 platform in 2008, with significant changes made to adapt it to the B2 platform.
Fundamentally the Anicolor consists of a zoneless short inking unit with a format sized engraved screen roller, a format size inking form roller and inking unit temperature control for rapid inking up and stable ink feed. According to the manufacturer the engraved screen roller ensures reproducible quality time after time.
“The principle is to use an anilox inking system with a chamber doctor blade instead of a conventional roller train,” explains Timson. “This allows the exact transfer of ink in every press revolution, resulting in consistent inking from sheet 20 onwards. The cylinders are all the same diameter meaning there is no ink fade on the printed sheet. Any minor changes to density can be made by variances in the temperature of the inking unit.”
Performance
The XL 75 Anicolor is quick, with a top speed of 15,000sph and rapid makeready times of around six minutes on a five colour press. It’s also incredibly flexible when you consider that it can compete with digital in the run length segment of 200 sheets and above (without personalisation), according to Heidelberg . At the same time it’s also cost effective on longer runs and easy to operate, says Timson.
“With full preset and automation in terms of a fully automatic simultaneous plate change and format presetting, it’s basically push button technology,” he adds. “It just needs to be backed up with a well-tuned pre-press with PCM and high-volume plate output capacity.”
As for quality Timson says it’s the “same as offset. Very consistent solids and vastly reduced colour variation. Thanks to the inking unit technology there is no colour change from the twentieth sheet to the ten thousandth.”
Development of Anicolor is continuing, LED and low energy UV version B2 Anicolor presses will be available later this year.
USP
Quite simply the unique selling point of the XL 75 Anicolor is that it’s unique – there is nothing else quite like this out there on the market (see alternatives for evidence). And that’s thanks largely to Heidelberg’s new ‘90:50:50’ formula, says Timson.
“This simply means 90 per cent less waste sheets with XL 75 and Anicolor technology. A 50 per cent reduction in makeready time compared to conventional offset presses, due to the anilox inking system and no requirement for ink density adjustment – even with colour and register inline adjustment tools. Finally this means 50 per cent higher productivity when both factors are considered.”
The numbers are compelling and make you wonder where this technology might best be employed in the future. Timson offers up one potential scenario: “Imagine the potential of a B2 press – say a 10 colour perfector – that can produce 8pp-A4 with 10 to 20 waste sheets with makeready times of five minutes. This is as close to digital makeready as it gets.”
Alternatives
It’s rare that this happens, but as Heidelberg claims the SM XL 75 Anicolor really is an exclusive beast. There isn’t a direct B2 sheetfed equivalent to the XL 75 Anicolor as none of Heidelberg’s competitors are currently using this technology.
Some B2 litho press manufacturer’s claim that their machines offer fast makereadies, but as one print industry stalwart says “with as few as 20 waste sheets on the XL 75 Anicolor, no one else can get close”.
For those printers who are keen to explore alternatives one possible option is the KBA Genius, which uses anilox inking, although unlike the XL 75 this is a B3 not a B2 press. Another potential option is the B2 HP Indigo 10000, which has the added benefit of allowing users to run variable data printing jobs. However, this digital machine is slower than the XL 75 Anicolor and it carries a significantly higher price tag.
Comment below to have your say on this story.
If you have a news story or tip-off, get in touch at editorial@sprinter.com.au.
Sign up to the Sprinter newsletter