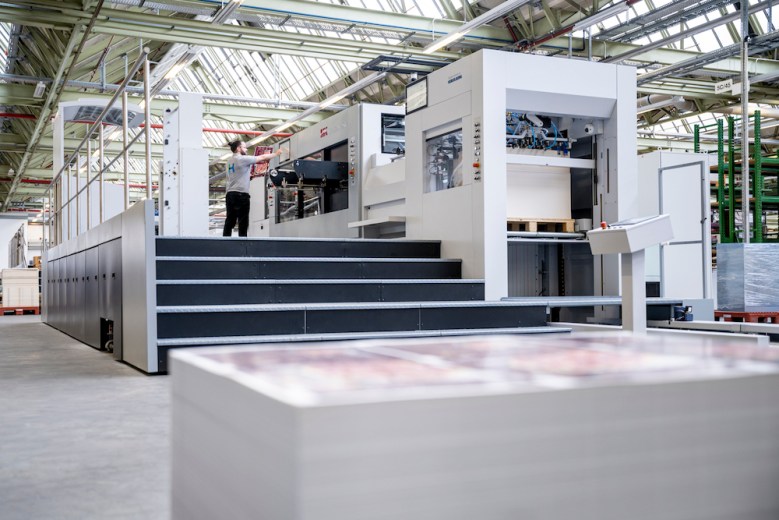
With packaging providing the industry with more opportunities, Heidelberg is increasing its play in this space with new product launches.
It has unveiled a new Mastermatrix 106 CSB, a new flagship die-cutter in collaboration with MK Masterwork with a production speed of up to 9,000 sheets per hour.
The machine is designed for high speed and fast make-ready times. For example, a new quick-lock clamping system for the cutting plate shortens the setup time without affecting tool compatibility with existing plates. The setup time is further minimised by MasterRake: the non-stop swords in the delivery are locked pneumatically and can be disengaged at the push of a button and moved by the operator. This shortens the setup time at the delivery by up to 70 per cent.
The Mastermatrix is integrated in the Prinect workflow. Job specific data is received at the die-cutter from Prinect. Data such as the sheet format is transferred and – after confirmation by the operator – the MasterFeeder sets itself automatically to the sheet format without further manual intervention.
During production, the MasterSet optical register system ensures perfect registration between the print image and cutting tool for each sheet individually with the utmost precision. The camdrive of the Mastermatrix ensures a smooth and quiet production.
Heidelberg has also taken the wraps off a new operating concept based on Heidelberg User Experience UX.
For example, the Speedmaster CX 102 from the new 2020 generation combines flexibility with navigated printing. It starts with efficient production planning via the Prinect Scheduler where production is optimised for multiple print jobs with the same or similar spot colours, materials, or die-cutting tools, and placed in the Job Queue of the Speedmaster CX 102 fully automatically and in the correct order – without manual intervention.
The Wallscreen XL guides the operator through the individual processes. With Intellistart 3, up to 50 upcoming job changes can be prepared on the press while production is underway.
Intelliguide navigates the operator through the complete job change and always selects the fastest makeready process. Intelliline visualises the process phase at the individual printing and coating units and indicates when and where a manual intervention is required. Assistance systems like Color Assistant Pro and Wash Assistant use artificial intelligence for continuous improvement.
For highly industrialised folding carton printers, Heidelberg has expanded the capabilities for the Speedmaster XL 106.
The new presetable CodeStar at the feeder ensures full traceability throughout the production. It marks each sheet with a unique number, barcode or batch number so it can be identified again at any time during production.
Another innovation is Hycolor Pro, the Speedmaster XL 106’s automated dampening system. The dampening solution is metered between pan roller and metering roller. The pressure/squeeze required for this purpose can now, for the first time, be controlled from the Prinect Press Center.
The operator can now quickly confirm the correct settings in all units – that saves time and effort while also enabling targeted corrections during production: The printer can address dampening issues on either side of the sheet. This results in fewer waste sheets at start-up and a more stable production run.
“The growth market of packaging and especially folding carton manufacturing are part of our core business. Our product portfolio is leading the industry, and we are introducing innovations to further enhance it based on our customers’ demands. The optimisation of folding carton manufacturing for the benefit of our customers is an integral part of our company strategy,” Heidelberg head f the folding carton segment Jörg Dähnhardt said.
Heidelberg has also mentioned that from mid 2021, Prinect Business Manager Packaging will be launched specifically for packaging printing. Together with the Prinect Production Manager and the tailored packaging add-ons, the result will be a fully integrated packaging workflow.
Comment below to have your say on this story.
If you have a news story or tip-off, get in touch at editorial@sprinter.com.au.
Sign up to the Sprinter newsletter