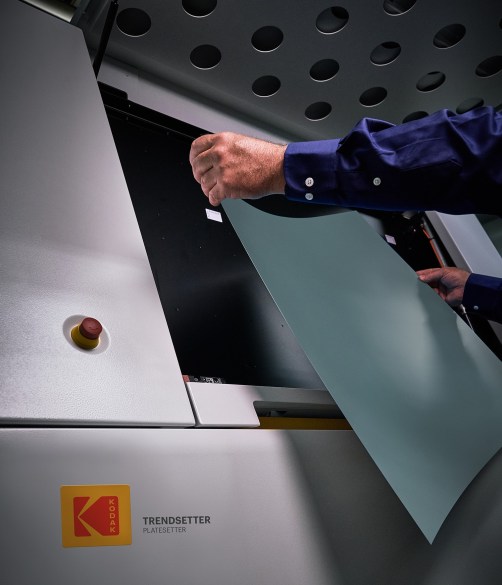
How good are your platesetters? What types of plates are you using? How does your computer-to-plate (CTP) work sync with prepress files going direct to digital print? Are there any knots in the system – black spots where double handling occurs – or bottlenecks where a slower process impedes a faster one upstream? These are the questions that every print enterprise needs to ask in order to remain productive and profitable in an era of narrowing margins and stiff competition for a shrinking slice of the commercial printing pie.
CTP platesetters
For Dierk Wissmann, Suprasetter 106, which Heidelberg rolled out three years ago, just keeps getting further ahead in the field. Heidelberg Australia/New Zealand (HAN)’s national sales manager says the 106 now comes with a pallet loader capable of holding various plate sizes simultaneously, resulting in increased output with a smaller production floor footprint.
Wissmann describes the Suprasetter 106, with pallet loader, dual cassette loader (DCL), ZAC processor and a fully automated Nela plate line, as “the ultimate no-hands CTP workflow available today”, which fits into Heidelberg’s ‘Push-to-Stop’ philosophy.
The pallet loader can hold up to 1,200 plates at a time, the DCL can handle up to 400 more plates and different sizes while the Nela plate line is fully customisable.
For example, customers will benefit from a barcode scanner that indicates data about which press the plate is for, which job it is, and even the number of the job signature. Using this information, the plate will then automatically pass to the inline plate bender and on to the designated stacker, guided by the barcoded data.
“The plates will then be stacked cascaded, so signatures are clearly visible for the printer,” says Wissmann.
“The stackers can then be rolled into the pressroom. This creates the benefits of immense time savings and error eliminations in the plate room.”
Bearing in mind the critical nature of platesetter componentry in keeping production on time and productive, HAN has introduced a 12-year coverage programme for laser heads on its Suprasetter, Wissmann said.
The Suprasetter ‘Ultimate 12’ programme advances existing Heidelberg programmes.
“The extremely high stability of our laserheads allows us to offer our customers a new programme called ‘Ultimate 12’, a 12-year laserhead coverage for Suprasetters ordered from April 1, 2018 onwards, subject to certain conditions. The Suprasetter ‘No Worries’ programme was launched in 2006.
For the latest in productivity, Currie Group’s managing director Bernie Robinson recommends the popular H-series CTP setters from CRON, which have optional integrated plate punching of up to two different punching types.
“The H-series is two thirds the size of the CRON F-series and has a slip sheet removal system built into it, plus a 50 plate auto plate loader as standard and is still a drum system,” Robinson says.
“The H-series has a range of different models available: the TP-26H, TP-36H, TP-46H, TP-60H and TP-72H series.”
Troy Neighbour, senior product manager, Graphic Systems, at Fujifilm Australia says his company’s offering of Screen CTP hardware is complemented by the unique features of Fujifilm’s ZAC processors.
“Our ZAC processors feature Fujifilm’s ZAC microprocessor control system, which helps achieve consistent, high-quality plate production with minimal chemistry usage and maintenance. When combined with our low-chemistry offset plates, printers get optimum performance while saving on water and chemistry,” Neighbour said.
“Our high-speed CTPs utilise Screen’s GLV technology, which allows a wider imaging swathe and a slower drum speed. The net result is a fast output with a very sharp dot.
“The platform itself is very stable and mature, and most R&D efforts are now concentrated around energy savings. Our latest devices are around 60 per cent more energy-efficient than the previous models.”
Screen’s managing director Peter Scott says the vendor’s ‘workhorse’ B1 CTP – the PlateRite 8600NII – now uses long-lasting fibre laser diodes. He says FLDs are not just more reliable but consume less electricity and enable faster writing speeds – up to 32 B1 plates per hour in the 8600 ‘Z’ model.
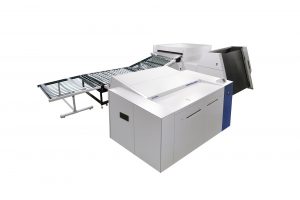
“Our VLF machines have also recently been upgraded to save energy, be faster and improve evenness of exposure using GLV (grating light valve) imaging,” Scott said.
“The new PlateRite Ultima 24000N 24-up series, for example, incorporates the latest GLV imaging heads with an upgraded optical system. These heads support the output of Screen’s proprietary Spekta 2 hybrid screening, enabling richer, high-resolution results. The 24000N-Z model is equipped with a 1,024-channel head that boosts output up to 35 VLF plates per hour, or 45 plates per hour when making B1 1030mm x 800mm sized plates.”
Scott says Screen is the world market leader in CTP, particularly in the 8-up B1 format.
“Our range is extensive and goes from the 4-up PlateRite 4600 series, through the 8-up PlateRite 8900/8600 models and up to the Ultima VLF range in 16, 24, 36, 40, and 48-up A4 page configurations. All are thermal machines, which Screen considers a superior technology and more environmentally friendly to violet.”
Screen also manufactures flexo/letterpress CTP devices (sold through Jet Technologies), in three formats from 870mm wide to 1,524mm.
Kodak’s newest Trendsetter and Achieve platesetters are highly energy conscious, says Rob Mollee, Australian and New Zealand sales director at Kodak.
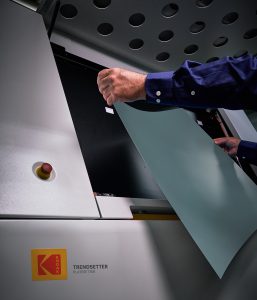
These setters use up to 95 per cent less power while imaging than similar competitive devices, helping printers reduce energy costs.
Also new from Kodak is the Multi-Pallet Loader (MPL) for the Magnus Q800 platesetter, which has a capacity of up to 2,600 plates in four formats.
To add more convenience for printers, Kodak introduced its Kodak Mobile CTP Control App, which allows printers to monitor and control up to 10 CTP devices from wherever they are, increasing uptime and productivity.
Squarespot technology is a cornerstone of Kodak CTP imaging, delivering stability, accuracy, and reliability, says Mollee.
The W-Speed option for Kodak’s Trendsetter platesetters can deliver a throughput of up to 75 plates per hour (four page) or 62 plates per hour (eight page).
“We’re focused on helping printers bring more speed, automation, and energy savings to help transform their prepress process,” Mollee said.
Agfa Oceania managing director Mark Brindley says Agfa’s Avalon N8-90, “provides an unparalleled imaging speed up to 70 B1/8-up plates per hour. Its state-of-the-art Grating Light Valve (GLV) imaging head technology produces exceptional imaging quality and tonal accuracy from corner to corner, plate to plate and job to job.”
The Avalon N8-30 joins the 8-up series in three speed variations (E, S, and XT). It offers options such as press punch blocks and can be matched to a single or multi-cassette autoloader for enhanced automation.
The Avalon B8-24 S/XT is “a robust entry-level output device with online or offline processing based on the reliable architecture and proven laser technology of the Avalon N,” says Brindley.
“For maximum productivity and autonomy, it comes with an optional automatic plate loader”.
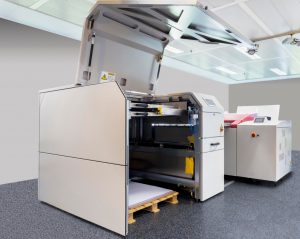
Scott Thompson, regional marketing and channels manager at Esko Australia, is excited about the impact on flexo printers of combining a setter and exposing unit.
“The combination of the CDI Crystal setter with the XPS Crystal exposing unit offers a perfect, consolidated flexo platemaking workflow, reducing manual steps by 50 per cent, errors by 50 per cent and operator time by 73 per cent,” Thompson said.
“Now with Esko’s Print Control Wizard software, a new level of simplification in the platemaking department is reached. No extensive knowledge of prepress or platemaking is required. Anyone can use the wizard to create premium flexo plates.
“The tool uses all critical print parameters and variables – imaging resolution, exposure settings, plate, substrate, anilox, press type and inks – to automatically generate the perfect screens and curves for each application. There’s no more need for platemaking experts.
“Businesses considering moving into the packaging and label markets can now benefit through Esko’s Packaging Simplified process, designed to bring best practised solutions to our customers,” adds Thompson.
Plates
Heidelberg exclusively distributes Fujifilm’s thermal and violet plates, including a broad array of process-free, low-chemistry and violet plates to suit a variety of printing workflows.
The Superia ZD plate offers a great process-free technology, Heidelberg’s Dierk Wissmann says.
“Heidelberg’s offering of Fujifilm low-chemistry Superia LH-PJE and LH-PLE plates and the award-winning Fujifilm intelligent ZAC processing system allows you to meet your environmental concerns and reduce maintenance at the same time.
“The Fujifilm ZAC system provides optimised processing quality by using intelligent developer replenishment. This results in a significant reduction in the volume of chemistry and water used, which helps you to reduce your environmental footprint. Should there be no special requirements in terms of very high run length (more than 150,000 impressions) or very high resolution (more than 200lpi), the process-free solution is an excellent choice,” says Wissmann.
Currie Group’s Bernie Robinson, whose company is the Australasian distributor for the full range of Agfa digital plates, as it has been for almost four decades, sees the Agfa TE direct-on press chemistry-free thermal plate for sheetfed commercial applications as providing clean-and-green operations, in addition to quality and user-friendliness.
Robinson notes that while Currie Group still has customers who use Agfa violet plates, as this plate is a hard and very reliable plate for their specific applications, they are being transitioned to CRON thermal CTP units to transfer them to thermal plates, when it is time for an update.
Troy Neighbour says Fujifilm’s Superia ZD is, “our longest running processless plate – designed for both UV and conventional ink – generating up to 150,000 impressions with conventional ink.
“With advanced scuff and scratch resistance through a number of high-performance multi-layer coatings, handling the plates is now easier and safer than ever.
“Our Superia ZD can maximise the efficiency of your offset plate production with the fastest route from platesetter to press – simply image and mount directly on the press. Being maintenance-free and with no processor, chemistry, gum or water, it also helps reduce running costs and downtime.”
He says Fujifilm’s processless plates offer UV ink compatibility to 50,000 impressions and avoids polluting of the fount. They provide a minimal run-up of sheets (less than ten).
But he cautions, “We see processless as only a viable option when you can keep your run-up sheets to a minimum.”
Fujifilm’s processless plates are just one choice among the vendor’s plate offerings, including low-chemistry and violet plates, to suit a variety of printing workflows.
“Low-chem plates when used with our ZAC processors can dramatically reduce printers’ resources associated with plate processing – water, chemistry, materials, labour and energy – helping printers improve profitability and productivity,” Neighbour said.
“All of our plates are manufactured with FujiFilm’s multi-grain technology, which allows printers to run less water on the plate due to its excellent water receptive characteristics. The end gain for the printer is better colour consistency and registration plus faster drying times. Our low-chem plates provide prepress with a more stable plate through the bath life, as well as minimal cleaning due to our innovative enhanced development layer, which means no sludge in your developer bath.”
Kodak’s Sonora X process-free plates represent a significant technology breakthrough in this field, notes Kodak’s Rob Mollee.
“With Sonora X plates, up to 80 per cent of printers are able to switch to process-free plates, including large printers and those with challenging printing applications that need a high-performance plate,” Mollee said.
Mollee says Sonora X Plates deliver three significant improvements over Sonora XP plates, including longer run lengths especially with UV applications, faster imaging speed, and more robust handling capability.
Sonora X plates are qualified for up to 400,000 impressions for heatset and commercial coldset and 200,000 for sheetfed applications, and 75,000 with UV applications (including conventional UV, low-energy UV and LED-UV).
Currently over 4,000 customers worldwide use Sonora plate technology and Kodak expects that nearly one out of three plates sold will be process-free by the end of 2019.
It also expects Sonora process-free plates to make up over 50 per cent of Kodak ANZ’s total plates sales which is ahead of worldwide trends.
Agfa offers a range of thermal and violet digital plates for the commercial, newspaper and packaging markets – for conventional processing, low chemistry processing, chemistry-free and processless, says Mark Brindley.
Launched at last year’s WAN-IFRA newspaper publishing expo in Berlin, Agfa’s violet chemistry-free Avatar V-ZH plate for newspapers has made an impact.
Its latest offering in thermal is the Energy Elite Eco plate, in combination with the Arkana smart processor.
Brindley says this no-bake, low-chemistry system offers customers great value.
In the thermal chemistry-free area, the Adamas plate and the Adamas clean-out unit completes Agfa’s thermal chemistry-free offerings.
Adamas runs chemistry-free with LED-UV inks, which Brindley says is a growing trend in sheetfed.
Agfa’s processless Azura TE, based on ThermoFuse technology used in the Azura chemistry-free series, offers high image contrast and good daylight stability.
Brindley says, “In the industry, we make a distinction between ‘processless’ plates, which are plates that are processed on the printing press, ‘chemistry-free plates’, cleaned by means of a gum, and ‘conventional’ plates, processed by means of high-pH developer.
“Our estimation is that the overall global market for digital plates from all suppliers is split 80 per cent to conventional plates, 15 per cent to chemistry-free plates and only five per cent to processless plates.”
While Screen does not make or sell plates, Peter Scott says its reseller/OEM CTP partners Fujifilm, Xing and Agfa do – and they offer processless plates.
When a CTP device is supplied for processless plate use, Screen technicians configure the laser diode imaging heads to suit the exposure characteristics of processless plates.
Workflow
Heidelberg’s Dierk Wissmann says Prinect can output to CTP and digital from the same workflow.
“Whether printers produce for commercial or packaging market segments, using CTP plates, inkjet or toner-based output devices, Prinect can drive them all,” he says.
The Prinect range is also available in the cloud, sold as Prinect Production Manager, and enables a low-price entry and covers the entire Prinect production workflow – from prepress modules, through offset and digital printing to postpress.
“The highlight is that with the Prinect Production Manager, you can configure your workflow in line with your specific requirements, and you only pay for your usage, irrespective of how large or small the system is,” Wissmann said, adding that if your needs change the configuration can be adapted.
Currie Group’s Bernie Robinson describes ElecRoc workflow from Founder Electronics as a fully integrated JDF/PDF prepress workflow with new system structure to achieve more stability and higher processing efficiency. It has a range of new modules and functions, a more intuitive interface, and is simpler to use. Job processing is also more secure and file management more straightforward.
He says Currie Group’s customers have found ElecRoc easy to use and scalable, meeting all prepress department requirements. It integrates the latest core technologies from Founder, providing the functionality required for job management, integrated JDF/PDF creation, preflight, trapping and imposition.
ElecRoc offers PDF colour management, 3D preview, EcoInk, hi-fi printing, PDF compare, cooperative task management, load balancing, zone screen, CIP4 ink control, advanced screening, colour/screen proofing, remote proofing, and output device support, says Robinson.
“ElecRoc combines automation with process control of the entire workflow in real time,” Robinson says.
He says ElecRoc smoothly integrates litho/CTP with digital production.
“It handles litho/CTP and digital software seamlessly. Our software is a drop-and-play workflow with check points all the way through the process,” Robinson says.
Troy Neighbour says Fujifilm’s XMF workflow now offers significantly higher ripping speeds, up to eight times faster than with conventional systems, a great asset as lead times shrivel.
Colorpath allows printers to set and monitor their colour and ensure they meet the latest ISO or Gracol colour standards.
“This is a simple and cost-effective tool that allows your prepress to control the process without having to outsource to a third party,” Neighbour said.
XMF is driven by the printer’s selected output device, regardless of whether it is litho or digital.
“You pass it through the same workflow and the output is then tailored to the device. For example, plates output as 1-bit TIFFs and digital can be anything from a flattened PDF to a JDF file which also presets certain parameters on the DFE.
“In addition to this, you can centralise all of your colour management within XMF via the Colorgate application, which allows you to output certified ISO or Gracol prints via offset or digital.”
Screen’s Peter Scott says Screen’s Equios is not just a CTP workflow.
“It functions as an overall solution platform for Screen GP’s devices and third-party equipment, enabling the control of CTP, digital printers, proofers and internet connectivity,” Scott says.
“Equios Art is a suite of technologies including Screen’s proprietary RIP, image processing and colour management systems, which combine to produce images of consistently high quality on diverse printed materials.
“Equios UX provides a broad range of functionality across the production process from Web2Print input to printing and finally postpress, resulting in outstanding quality and productivity, with minimal operator skill requirements.”
Scott says the latest v6 of Equios incorporates Adobe’s PDF Print Engine 4 and Library and the latest version of PitStop for enhanced preflighting.
As to litho/CTP-digital crossover, Scott says, “Equios allows multiple and different types of devices to be operated from a single user interface. It integrates years of know-how for prepress technology, with functions that enable fully automated CTP workflow and high-speed print-on-demand digital variable printing.”
Kodak Prinergy delivers powerful automation customised to individual print shops, no matter what CTP or press a printer uses, says Kodak’s Jek Sin Hiong Sim, sales director of APMEA Kodak Software Division.
The Prinergy Device Track, with Job Ticket Editor, features seamless bi-directional JDF communication with Kodak XPO/PC and CTP devices.
“By reducing manual touchpoints, Prinergy elevates productivity, all while delivering output that is as highly tuned as it’s high-quality,” says Sim.
With Prinergy’s Rules Based Automation, the guess work is taken out, says Sim. If the flow of the print production provides a quantity of print pieces needed, the RBA rule could simply apply an ‘if… then’ principle. For example, if a job is greater then 500 pieces, the RBA would stipulate that it should go to litho/CTP.
The system then presents the steps – imposition, proofing, plate-ready files. If the job was less than 500, the RBA would send it to a digital process.
“Now all a user has to do is send the files and job details,” says Sim.
“The rest is pure automation.”
WRH Global offer Kodak plates, including Sonora DOP (Develop-On-Press) plates, Kodak Magnus, Trendsetter and Achieve CTP setters and Screen PlateRite setters. It also offers Kodak Prinergy and Screen Equios workflows.
Ian Martin, general manager, trade, at WRH Global Australia, says his company offers both thermal and violet plate technologies, although thermal now clearly dominates, except in some older newspaper installations, as it provides a platform for the future with DOP.
“We have evaluated a number of DOP technologies over the years with mixed success. This is largely due to the diversity of press types and conditions in the market. We found that the age, condition and maintenance programme contribute directly to the success of running DOP. In recent years, improvements to plate coatings, visibility of latent image and handling robustness have improved significantly to the point where we are currently testing a DOP plate with very promising results.”
Agfa’s Mark Brindley says the Apogee workflow – now in v11 – automates virtually all prepress tasks, with the system now offering multi-product support to increase printing efficiency, while integration with PressTune supports Agfa Graphics’ ECO³ market approach on economy, ecology and extra convenience.
The ECO³ programme, besides offering chemistry-free plate technologies that eliminate wastage, features PressTune and InkTune, two software modules that enable printers to improve their processes and become more productive.
PressTune maps a quicker route to a first sellable copy by reducing start-up waste, while Inktune allows a significant reduction of ink consumption without diminishing image quality. Apogee v11 “offers a mechanism to combine print jobs in an intelligent way in order to optimise press time, while also keeping track of the actual order”.
Comment below to have your say on this story.
If you have a news story or tip-off, get in touch at editorial@sprinter.com.au.
Sign up to the Sprinter newsletter
It’s interesting that all the various workflow solutions do provide some great features and functionality. However often there are some areas of weakness in the “holistic” approach to file management, flight checking, approval and imposition. That is where some of the independent solutions help supplement and add value. Such as Enfocus for PDF preflight and correction, alongside their Switch workflow. Impositions products that provide rules based or AI dynamic ganging can make dramatic savings and efficiencies too across a diverse range of devices and processes.
A modular approach also ensures you can easily integrate with many of the propriety solutions featured here.