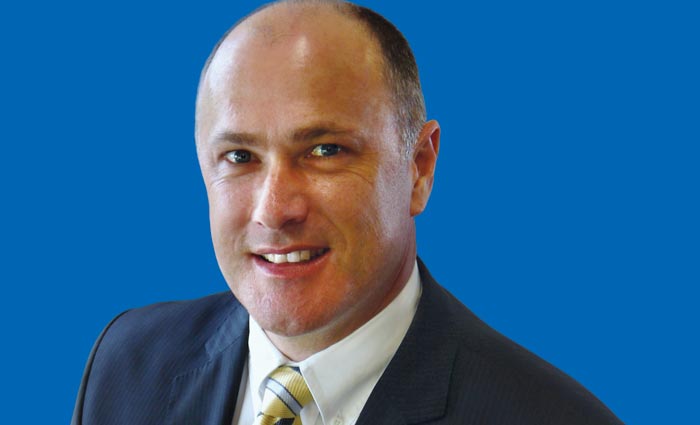
This article was first published in the November 2020 issue of AP – By Screen GP Australia managing director Peter Scott
Today’s prepress sector consists mostly of file preparation and workflow, whereas it was once a multi-step mechanical process using film, scanners, step-and-repeat and exposure devices. Such files – mostly PDF – remain as digital data now, up to the point of sending to output devices such as CtP setters, proofing devices or direct to digital presses. Prepress operators today can perform most of the old prepress functions on their computers.
Prepress houses were once separate and highly successful businesses servicing printers with film, proofs and sometimes plates. With the introduction of CtP, it has moved in-house. PostScript PDL and DTP were the cataylsts that led to this. Prepress is now far more automated with JDF/JMF integration with MIS and Web2Print systems and CIP4 output to post-press, allowing for maximum automation and efficiency.
Software, plates and platesetters are a huge part of prepress. Without software such as Adobe’s Indesign, Illustrator, Photoshop, and PDF, and workflow such as Screen’s EQUIOS to prepare the print-ready files or add VDP, there is nothing to send to the CtP setters.
Screen has remained the world’s largest supplier of CtP devices in all formats – from B2 up to 48-page VLF. We do not supply printing plates as we leave that to our reseller partners such as Fujifilm, Agfa and Xing.
Screen’s prepress solutions provide a robust, efficient and well-supported (through our online Trust network service), method to maximise press productivity – digital, offset or flexo – and can therefore add profit to the bottom line by resolving bottlenecks and manual intervention.
Screen’s new generation of PlateRite thermal CtP setters use less power, are faster and have long-lasting and stable Fibre LED lasers instead of the old gas lasers. They are very environmentally sound machines, especially when process-less plates are imaged.
The top-seller is the PlateRite HD8900N which comes in three speed versions, making up to 70 B1 (8-up) plates per hour. Screen’s EQUIOS workflow platform allows multiple different types of devices to be operated from a single user interface and includes Screen-developed innovations such as Spekta screening, output to third party POD, LabProof proofing and also EQUIOS Online which connects the customer, designer and printer.
Within the prepress sphere, printers can find value in CtP as it has never been more affordable. When introduced around year 2000, CtP devices were expensive; in some cases, almost as much as the press. Today, they are much more affordable and also more efficient and lower in cost to run. Combines plate-supply and CtP upgrade packages from our resellers can mean that the value is outstanding.
With all printers already in prepress in one way or another, I can only say that it is important to deal with reliable suppliers who back up their products with local support. Screen has been in prepress innovation for over 70 years and we are the last of the ‘big four’ of digital prepress pioneers that saw the industry transition from analogue to digital from the 1980s and now we are part of the Industry 4.0 and IoT transition.
Precision engineering – mechanical and digital – are our hallmarks, which is why Screen is the major supplier of silicon-wafer solutions to the computer chip sector. There is a little bit of Screen in just about every electronic device made in the world. Prepress to us is an extension of this precision and also, because it is where we began before computers, the sentimental favourite within the company.
Moving into the future of prepress, plates will continue for a long time yet, so CtP devices will continue to be installed. The destiny of the rest of prepress is probably to become more automated and assimilated into the normal day-to-day running of any printing business. In effect, it will be there and more powerful than ever – but less visible!
Comment below to have your say on this story.
If you have a news story or tip-off, get in touch at editorial@sprinter.com.au.
Sign up to the Sprinter newsletter