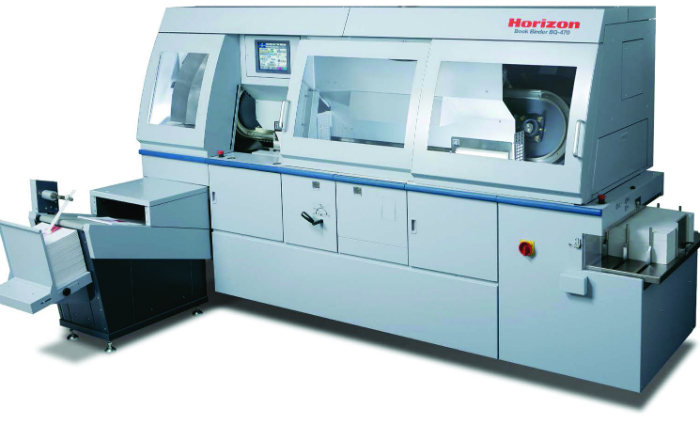
AUTOBOND INKJET SPOT UV
This spot UV machine from Autobond has a row of seven inkjet printheads that digitally print drop-on-demand LED curable spot UV varnish onto matt OPP laminated sheets.
The machine consists of an Autobond conveyor table built. The conveyor table is split into two sections — the first half consists of a series of angled side-shift rollers which move the sheets into a side-lay for registration (similar to a folding machine), and the second half consists of a driven vacuum belt which holds the sheets completely flat all over.
There is a high-speed, electronic contrast sensor that detects a mark or line printed on the front of the sheet, which registers the sheet’s speed and the distance it’s travelling in relation to where the inkjet heads are to print the varnish. When the sheets are flat, the inkjet printhead bar prints the varnish in the correct pre-determined area of the sheets. There is as little as one sheet makeready, because an 8-bit, 360dpi greyscale bitmap (BMP) image file of the print job, formatted for Microsoft Windows, is downloaded to the software controlling the inkjet printheads.
The inkjet printheads themselves are 25mm deep x 100mm tall x 490mm wide. The sheets then continue along the vacuum feed table and pass under a low-energy, cold curing, ozone-free LED lamp, which cures the varnish, and finally delivers the sheets into the stacker. Maximum speed at 360dpi is 36 metres/ minute, or 12 metres/minute at 720dpi.
SPECS AT A GLANCE:
Conveyor table size: 2.5 x 1.02 x 1.1metres; 20mm thick side-plates
Number of printheads: 7
Max speed: 35m/min @ 360dpi; 12m/min @ 720dpi
DUPLO DC-646 DOCUCUTTER
Duplo equipment is distributed in Australia by Neopost Australia, who considers the primary market for the DC-646 DocuCutter to be digital printers of all persuasions.
The DC-646 can slit, cut, crease and perforate in a single pass, which allows users to feed an SRA3 sheet to produce 21 to 24 finished business cards. It can also handle six-up DL flyers, gift cards ready for folding and posting, as well as time perforated tokens and similar products.
As with all the company’s commercial range of products, Neopost Australia includes a standard one-year onsite agreement with training. It also offers up to an additional four years’ coverage for parts and labour.
Neopost also offers in-house finance, and can work with many of the market’s leading lenders. The standard machine with delivery, installation and training, including a one-year Onsite Service Agreement, is approximately $1,000 per month ex GST.
SPECS AT A GLANCE:
Operating speed: 30ppm (A4 LEF 2 cuts, 1 crease)
Operating system: Multi-language Windows based PC controller software and control panel
Job memories: 80; unlimited memories on PC controller
Feeder capacity: 100mm
Paper widths: 210-370mm
Paper lengths: 210-670mm
Minimum finished size: width 48mm; length 50mm
Paper weights: 110-350gsm
Tolerance: +/-0.2mm
Slits: 6 (standard); 8 with optional module
Creases: Max 20 per sheet
Cutter (cross-knife): Max 25 per sheet
Receiving stacker: 140mm
Card stacker capacity: 60mm.
FERAG IN-LOG RT3080
While Ferag’s traditional focus is largely in the high-end finishing/ mailroom market, to address the growing digital sector the company has partnered with several companies, including In-Log, which offers a range of different solutions.
Ferag has the ability, with the cooperation of trade partners, to offer the full gamut of in-line finishing requirements, such as trimming, stacking, wrapping, strapping and conveying, backed up by Ferag’s service team.
In-Log, a subsidiary of Merten Maschinenbau und Vertrieb, is a Vienna-based manufacturer of complex print finishing and mailroom duties such as conveying, waste paper administration, trimming, personalisation, stacking and palletising. In-Log combines over 30 years’ experience in the development, manufacture, service and distribution of print finishing systems. Ferag Australia is the exclusive distributor of In-Log in both the Australia and New Zealand markets.
In-Log’s equipment comprises a diverse range of solutions specifically focused on conveying, trimming, stacking and palletising.
More recently it has tailored a range of in-line solutions for the high volume digital printing market, which can be personalised specifically to each customer’s pagination, formats, production speeds and the like. Trimming can be on a rotary two-knife set-up, and grow from there into multiple head and three-knife configurations. Additional products such as a centre slitting unit add extra functionality.
The In-Log stacking options range from 20,000 up to 100,000 copies per hour, and can be configured to support entry-level book binding through to high-end digital finishing solutions such as that offered by manroland web systems FormerLine and FoldLine digital folders.
SPECS RT3080 AT A GLANCE:
Operating speed: Max 80m/min
Paper weight: Handles up to max web paper thickness
Format: Min 100mm to max 550mm1
Power: 14000 watt
GMP PROTOPIC QUATRO SLIT LAMINATING MACHINE
The new range of laminating products from Korean manufacturer GMP is distributed through Renz Australia.
Laminating is an important element in the enhancement and protection of digitally print, and for the reproduction of photo prints and photo books. The GMP Protopic Auto Quatro Slit is an example of the flexibility and new revenue opportunities in one machine.
Aimed at the on-demand digital market this automatic laminating machine provides four embellishments to digital print. These include single and/or double sided lamination/celloglaze; single and/or double sided photo matt texture embossing; digital sleeking, producing a range of full sheet or spot effects with foils, gloss or matt coatings; and a patented GMP Slit–Book technology which produces an inner book block for lay flat photo books.
Apart from traditional laminating and celloglazing the GMP Quatro range provides the ability to produce photo prints (silver halide replacement), photo books and photo calendars to a sector of the market that is booming.
The Protopic Auto Quatro models also provide additional finishes and embellishments to offer print customers.
GMP silver halide replacement produces photo prints that look and feel exactly like traditional silver halide photographic prints. This technology, invented and patented by GMP in partnership with HP Indigo, reduces costs by 50 per cent or more compared to traditional silver halide photo production, and has clear environmental advantages.
Digital Sleeking is an easy way to achieve special effects such as spot varnish, metallic foil stamping and holographic effects in-house. The process involves a special image transfer that bonds specifically to HP Indigo inks and other digital toners applied in spot locations, or to the full sheet creating a wide variety of special effects and designs.
The GMP Slit-Book system produces the inner block of a lay flat photobook. The slit book solution comprises a pre-bonding and in-line guttering device that creates the book hinge prior to lamination. Compared with most existing solutions Slit-book can produce a lay flat book block at a lower cost with greater choice and flexibility in different finishes.
A fully optioned Protopic Auto Quatro Slit can be financed for $350 per week, including delivery and installation. Comprehensive training is provided, with ongoing operator and technical support available nationally.
SPECS AT A GLANCE:
Operating speed: 3m-15m per minute
Max Paper size: 540x800mm
Paper weights: 120 – 320gsm
Warm up time: 7 mins
HORIZON BQ-470
Supplied by Currie Group the BQ-470 EVA PUR binder enables a fully automated setup through an intuitive icon based LCD touchscreen for book-binding up to 65mm thick. It features a customer replaceable glue tank unit for both EVA hotmelt and PUR hotmelt adhesives; simplified and accurate changeover to produce professionally finished books; two large application rollers for strong, high-quality binds and a separate side glue tank; and an automated elevation conveyor that can stack books up to 300mm high.
Claiming a maximum cycle speed of 1350 books per hour with EVA hotmelt glue, the BQ-470 has sliding windows for safe access and a clear view. It offers three milling styles: milling off, milling for EVA, or milling for PUR. It also offers an option for automating the bindery with JDF workflow, using the pXnet bindery control system, which can consume JDF data for fully automated setup, or act as a control point to schedule work, send job data, and collect statistics from networked machines in real time.
The Standard Horizon BQ-470 fully-automated four-clamp perfect binder, with its state-of-the-art design and fully-automated setup, is easy to operate with minimal operator training required. It produces perfect bound books, with four clamps that travel on a vertical elliptical track. The BQ-470 is the latest in an expanding line of products that draw on Horizon’s core competence in finishing automation. The BQ-470 binder’s 10.4” LCD touch-screen is used to provide stepper motor-controlled automation to the professional-quality mid-range binding market.
The BQ-470 can bind books up to 2.5” thick, and interchangeable glue tanks support both EVA and PUR adhesives to meet varying customer requirements. The BQ-470 perfect binder fits a sweet spot in short-run professional-quality book production with full automation and touch-screen control. And the ability to swap-in a PUR glue tank lets the BQ-470 serve an even wider range of applications, including digital color books.
SPECS AT A GLANCE:
Throughput: 1350 books per hour
Clamps: Four
Max thickness: 65cm / 2.5”
Glue: PUR and EVA
MORGANA DIGIFOLD PRO
The Morgana DigiFold Pro, distributed in Australia by Ferrostaal Australia, is considered to be ideal for small digital printers right through to large offset printing companies.
DigiFold has been Morgana’s flagship product since its introduction in 2001. In the latest version the speed has been increased by 20 per cent, and Morgana has added a touch screen, as with all Morgana Pro models, which allows the operator to control all the functions of the machine. Set-up takes seconds, and can be as simple as pressing three buttons — stock size, fold type and the GO button. The alphanumeric memory allows jobs to be named and saved, and with a simple search function allows them to be quickly retrieved.
This versatile machine has several uses, including as an integrated creaser/folder performing both functions in a single pass, as a “stand-alone” creaser when folding is not required, and as a perforator when neither creasing or folding is needed.
The machine’s increased speed now makes the DigFold Pro a viable proposition for litho printers who suffer the same cracking problems as digital printers. Using Morgana’s patented “flying knife” technology, they can ensure that there will be no scuffing or marking on digital stocks that are caused by using conventional folding methods.
Additionally, Morgana’s DynaCrease mechanism will give the same non-cracking crease without stopping the sheet, significantly improving productivity.
The price includes delivery, training and 12 months’ warranty, both electrical and mechanical.
SPECS AT A GLANCE:
Fold options: Single, double parallel, engineering, gatefold, closed gatefold, letter, concertina
Max speed: 6,000 sheets/hour
Dimensions: L 1980mm x W 655mm x H 1265mm
Sheet size: 700mm x 385mm
Sheet Weights: up to approx 400 gsm including laminated material
NAGEL DFC
According to the Australian distributor of Nagel products, Paper Handling Equipment, the Nagel DFC represents a highlight of modern cutting technology.
The DFC offers numerous applications which have until now only been provided by much bigger and more expensive machines. PHE says the DFC is an ideal solution for digital printers with small or medium size jobs. The DFC is capable of producing unusual boxes and packaging, pharmacy cartons, presentation folders, CD covers, labels and much more.
The Nagel DFC processes paper and cardboard up to 450gsm as well as many plastic materials. Die-cutting, perforating, creasing, embossing and kiss cutting can all be performed on the DFC.
The principle of the machine is based on a high-quality magnetic cylinder, a conveying cylinder and a flexible die-cutting form. The die-cutting form is produced according to the customer’s specifications and can be used up to 100,000 times.
The DFC 450 can take a maximum sheet size of 500 x 430mm in stocks up to 450gsm. It can run at speeds up to 2,300 sheets per hour. According to Nagel, the set-up time is less than three minutes, with a touchscreen display that provides easy menu navigation and set-up. Nagel says there is no need for trade qualified staff to operate this die-cutting machine, which is a great advantage over traditional die-cutting methods.
PHE has Nagel trained staff to install and train new staff on the DFC’s operation. This machine can be purchased from just $351.00 per week.
SPECS AT A GLANCE:
Sheet formats (L x W): 160 x 90 – 500 x430mm
Paper weights: 45 – 450gsm
Max speed: 2,300 sheets/hr
Height of stack on feeder: 60mm
Die cutting accuracy: up to +⁄- 0.2mm
Max set-up time: 3 minutes
Waste paper: 3-5 sheets
Refilling while in operation: Standard
PLOCKMATIC SYSTEM AF2000
In today’s demanding printing environment, a flexible solution to booklet production is a must for all digital printers. Often there is a need to merge jobs from more than one digital print device or to add colour, laminated or coated covers to finish a booklet. There may also be a requirement to finish booklets from several digital devices, where an inline solution on each machine may not be a cost effective solution.
The Plockmatic System AF2000S uses a high capacity dual bin feeder to offer a flexible solution for a wide range of booklet types and sizes. The system is fed by the AF602 air assisted feeder, which has a loading capacity of up to 540mm for long, uninterrupted production runs. Pre‐collated sets can be placed into both bins for longer runs, or covers can be placed into one of the bins when they need to be merged with collated sets.
The booklet making section can be supplied with heavy-duty stitching heads for up to 50,000 stitches from one wire spool, or with stapling heads which can be loaded with 5,000 staple cassettes. A fore‐edge trimmer gives a clean finish to the open face of the booklets.
An optional Squarefold can be added to the system to produce a squared spine, flat book to give the effect of a perfect bound finish.
For full bleed production, the CST crease and side trim unit can be added. Trim edges can be removed from the sheets so there is no need to trim the sheets prior to production in an offline guillotine.
The Plockmatic System AF2000/ AF2000S offers versatile configurations and options to provide a flexible solution to digital booklet production needs.
Plockmatic offline booklet makers and feeders are distributed in Australia and New Zealand by Fuji Xerox Supplies Division.
SPECS AT A GLANCE:
Feeder bins: Air-assist dual bin feeder unit
Loading capacity: up to 540mm; feed pre-collated sets from digital devices
Product thickness: 30 x 80gsm sheets, booklets up to 120 pages
Max speed: Up to 2,400 books per hour
Options: Stapling head and stitching head versions; front edge trimmer unit; SquareFold module
TEC UV COATER
Konica Minolta has announced the introduction of TEC UV coaters to the Australian market.
TEC Lighting is a global leader in the design and manufacture of UV lamps, curing equipment and special energy sources, with over 100 years’ combined experience. TEC Lighting’s approach to engineering and development led to the company’s partnership with Konica Minolta Australia.
Konica Minolta Australia has ordered its first shipment of the 16-inch (40.6cm) wide UV flood coater units, a combination of in-line and automatic feed units that the company expects will meet all the requirements for digital cut sheet coater production for commercial print customers.
Both units are designed with high performance in mind, with the ability to coat sheets at speeds up to 4,800 sheets per hour. Both offer the unique TruCoat Technology, with the coating solution available in matt, satin or gloss, depending on requirements. These coatings have been specifically designed for Konica Minolta print output, and have been tested intensively in the American market.
As with all its production solutions, Konica Minolta Australia will supply training for operators to use and maintain the system. Two hours of training is all that is required to get operators up and running, says Konica Minolta Australia.
These systems will be supplied with 12 months’ parts and labour warranty on non-consumable items. For the second year onwards, Konica Minolta Australia has several offerings to suit, depending on the service coverage required — these include labour only or a comprehensive parts and labour service that will incur an annual charge. There is a dedicated Customer Helpline currently for production customers, and this will be expanded to cover the TEC UV coaters.
Konica Minolta can offer finance to approved customers wishing to purchase the TEC UV coater, and can offer a competitive finance package. The Inline model, TEC TRUVIL16, is available for around $36,000.00 ex-GST, and the Auto Feed Off line system will be under $40,000.00 ex-GST.
Both systems are provided with a starter pack, delivery, installation and training so that operators can quickly be running jobs effectively.
SPECS AT A GLANCE:
Max sheet size: 400mm x infinity
Sheet thickness: 150-600gsm
Operating speed: up to 5,500 sheets/hr
Coatings available: high gloss, satin, matt; textured coating rollers also available
Compatibility: Digital and offset compatible; connects inline with bizhub systems and Kodak NexPress
Applications: Business cards, direct mail, book covers and sleeves, greeting cards, menus photos and posters, point of sale, marketing collateral
WATKISS POWERSQUARE 224
An innovative complete book making system for digital and offset print applications. It is available in three configurations to suit different workflow: online, nearline and offline.
In a single machine it combines the four processes of stitching, folding, spine forming and trimming to produce SquareBack books up to 224 pages thick. It features fully automatic settings for different book size and pagination, including variable stitch-leg length for varying book thickness.
The maximum book thickness is 10.4mm (208 pages 80gsm, 224 pages 70gsm), double that of alternative conventional booklet making machines, so it is suited to higher paginations or to thicker stocks. This makes the Watkiss PowerSquare 224 a fast and cost effective alternative to perfect binding or tape binding. Digital print applications frequently use heavier stocks and need the flexibility to produce a wider range of finished books from a single process, with little or no operator intervention – the Watkiss PowerSquare is a match.
The PowerSquare is a single solution for books from 4 – 224 pages. The finished SquareBack books have the square-spined appearance of a perfect bound book, but with the security of a stitched spine. They lie flat and are easy to pack, stack and handle. There is no risk of loose pages and you can print on the spine.
The PowerSquare has a single stitch head which inserts one to six stitches in the spine of the book. The stitch head and clincher are static the sheets move to the stitch, not vice versa. This means the stitch head and clincher never have to be moved, so alignment and stitch quality is consistently good.
SPECS AT A GLANCE:
Max book thickness: 10.4mm
Pages: 4-224
Page sizes: 200 x 203mm to 364 x 500mm
Stock thickness: 60-250gsm
Comment below to have your say on this story.
If you have a news story or tip-off, get in touch at editorial@sprinter.com.au.
Sign up to the Sprinter newsletter