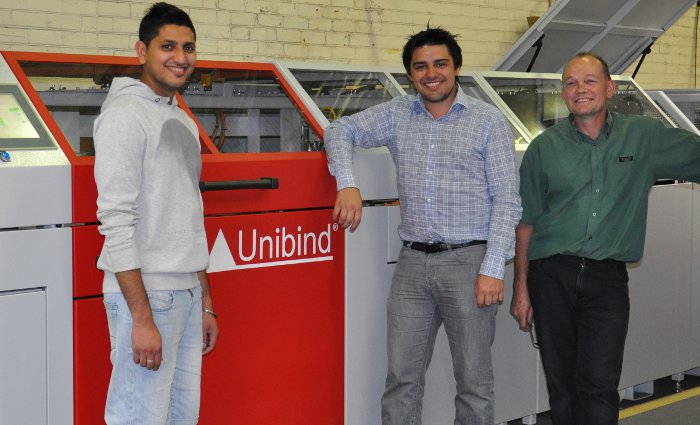
Describe your business
Photobook Shop has 24 employees and we sell online photo products, such as photobooks. We started as digital commercial printers and started making photo-gifting products in December 2010.
What have you bought?
We purchased a Unibind CaseMaker 750A in 2011. Before the CaseMaker, we had the Fastbind system, a cheap entry-level system. It was soon clear we would soon outgrow the Fastbind system as our business grew. To complement the CaseMaker, we have recently purchased a Unibind BCC10, which has automated the book binding process. This means we have dramatically increased productivity without having to increase staff numbers. We are the only company in Australia with a Unibind CaseMaker and a BCC10.
What does it do?
The CaseMaker is a totally automated machine that wraps a custom printed sheet around a plain CasePlano. The CaseMaker uses dry adhesives, which has eliminated spoilage caused by application problems from using wet glues.
Why did you choose this product?
Even though we were manufacturing low numbers of books when we first started, we would constantly receive complaints from customers telling us that their books just weren’t holding together. There were issues with them being pulled apart or damaged when dropped so we felt that the books needed to be more durable. The Unibind covers have a steel spine, which was much stronger than the boxboard spine we were previously using and this was a big factor in choosing the Unibind CaseMaker. Some 4,500 books were manufactured last month with very few problems. We also knew the CaseMaker would cope with a dramatic increase in manufacturing output as business grows.
Did you consider any other products?
We looked at the Kolbus, which is a big, expensive machine but not designed for variable jobs. We looked at various other systems, but the Unibind product and the stronger spine that kept the CaseMaker as the best option.
What features do you like most?
The CaseMaker is quick. We can set it to run really quickly or we can run 10 books then slow it down to make sure the quality is what we want. Changing over from one size to another size takes about 15 minutes, which is not too bad. As we run six different sizing formats, this is important to us.
Is there anything you wish it had that it doesn’t?
As far as hardware, there is talk that the book cover process and binding process may be combined into one system, which would be great. It would also be an advantage to us if we could improve the changeover times from the current 15 minutes. This may be possible as Unibind are always looking at ways to improve the machines. We recently had a visit from Unibind staff from Belgium who installed updates, both hardware and software.
How fast is it?
It manufactures 350 to 400 covers per hour depending on book size.
How reliable is it?
Very reliable. All machines have a hiccup here or there but the service is fantastic. Unibind are usually here within 30 minutes and have the machine going again soon after, which is what is important.
How easy is it to use?
As an example, our new operator joined us about three months ago and he took around a month to get up to speed. It seems like a long time but the machine is very technical and he didn’t have an extensive background in the book binding industry. He had a carpentry background.
Has it saved time and money?
It made an enormous difference to us. When we began manufacturing books, we could only make 20 to 40 covers per hour depending on the skill of the operator. This machine manufactures 10 times as many. It has enabled us to dramatically increase productivity.
Were there any difficulties surrounding the install?
The biggest difficulty was that the machine came from Belgium. Technicians had to fly out from Europe for installation. They now have technicians locally.
Would you buy another one?
Yes, we would. We have just commenced doing business-to-business corporate work and we can easily cope with 10,000 to 15,000 business covers per month. However, as business keeps growing as it has in the past 12 months, we cannot discount the possibility of needing a second unit.
Supplier’s response
Photobook Shop came to us in January 2011 looking for a solution to make case-bound hard books. We arranged for them to travel to Europe to investigate working installs of the Unibind 750A case-making machine. Upon viewing, Peter’s decision to purchase the system was an easy one. He was impressed with the speed, accuracy and that highly skilled operators were not required to operate the machine. It was installed with two weeks of training provided by our technicians from our Belgium head office. Since install, it has been astounding to see Photobook Shop grow from a business in its infancy, to a major supplier and brand.
Frank Tevere, Unibind
Comment below to have your say on this story.
If you have a news story or tip-off, get in touch at editorial@sprinter.com.au.
Sign up to the Sprinter newsletter