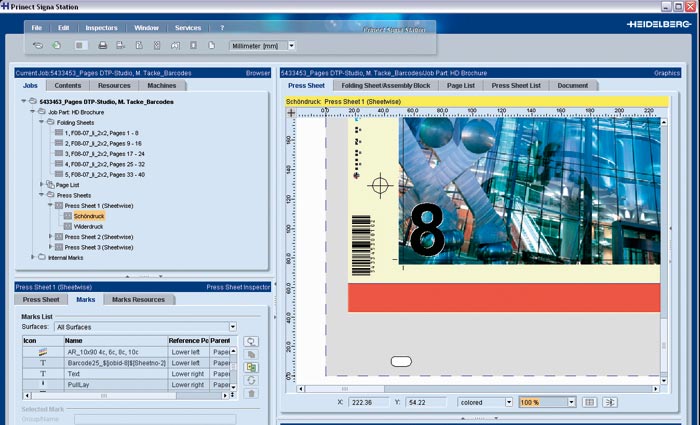
What does it do?
Heidelberg claims to be the only company that can offer an integrated design-to-finishing packaging solution. The entire process is linked seamlessly together by its Prinect workflow modules. Although Prinect is now an established brand, its entry into the packaging space is still developing, albeit rapidly.
When was it launched?
The first incarnation had its debut at Drupa 2008, and has developed at a rapid rate. The product is part of the press giant’s move into packaging, a journey that has seen it acquire Jagenberg, which developed its Dymatrix/Varimatrix die-cutting and Diana folder–gluer range.
Who is the system targeted at?
According to Soeren Lange, product manager of Prinect workflow at Heidelberg ANZ, Prinect for packaging is targeted at three groups: commercial printers that produce some packaging work; packaging converters that have anything from a sole production site to two or three; and large packaging businesses that could have an international presence.
What is its USP?
Lange says: “Prinect uses the same database across the entire production chain, which means automation, data integrity and production transparency can be pushed to the maximum. Print buyers can be tightly integrated and approval cycles can be automated. Most packaging printers run standalone products that require a lot of manual work and certainly don’t interact with each other. Those guys can now implement workflow smarts, reduce errors and speed up production.”
What are its other main features?
According to Lange, the product that has the most impact is the Prinect Signa Station Packaging Pro imposition and planning tool, which combines the structural design of the carton with the graphics. All colour marks, colour bars, control and printing marks plus numbering for one-ups and waste areas are added to the sheet. The tool can import and export CAD format, step and repeat work and create ganged-up jobs, which, the vendor claims, makes best use of the plate and minimises paper waste.
How easy is it to use?
Lange says Prinect is very easy to use. “Naturally the technical knowledge required increases with more complex configurations. However, as Prinect is one system and looks similar in all production areas, it’s easier to cross train and repurpose data in other areas.”
Lange says there are hundreds of possibilities with Prinect, while jobs that require spot-colour expertise, such as packaging for hair colouring variants, would require a trained pre-press figure.
What about training and support?
Heidelberg ANZ has just trained local experts who will install, train and maintain the system. Training can be on site or in Heidelberg’s Print Media Academy depending on the requirements. After several days, the customer is left to get to grips with the system before Heidelberg returns to carry out more advanced training while tackling issues that have arisen. On top of that, Lange says, delegates can also attend additional training at the manufacturer’s Print Media Academy in Germany.
How much does it cost?
Due to its modular nature, the starting price is dependent on configuration.
Specifications
Prinect prepress modules include
• Prinect Package Designer
• Prinect PDF Toolbox
• Prinect Prepress Manager
• Prinect Signa Station
Prinect press modules include
• Prinect Easy Control
• Prinect Image Control
• Prinect Inpress Control
• Prinect Inspection Control
• Prinect Press Center
Prinect post-press modules include
• Prinect Postpress Manager
Contact: Heidelberg Australia & New Zealand, 1300 135 135, www.au.heidelberg.com
The alternatives
Esko
Esko’s products comprise editing and sheet layout, colour manage-ment, online collaboration, output, imaging, workflow automation and MIS and ERP. Peter Henderson from Esko Australia says the tools that most suit this market are its DeskPack plug-ins, which have brought high-end processes such as barcodes, trapping and white underprint to the desktop. He also points to Automation Engine 10, which uses JDF and automates the repetitive tasks in pre-press, and also links to Web Centre, which is Esko’s web-based approval system.
Contact: Esko (03) 9544 1117, info.asp@esko.com
Manroland
Printnet comprises the firm’s entire collection of workflow tools from administration to press production for its sheetfed presses. Job admin is handled by PressManager, which automatically prepares jobs while performing technical pre-settings. The ColorPilot ink measuring and control system measures print control strips at 25cm per second, allowing for densitomet-rical and colorimetrical values to be measured at the same time. InlineInspector helps promote waste reduction by detecting faults early on, allowing the operator to react immediately.
Contact: Manroland (02) 9645 7900, www.manroland.com.au
Comment below to have your say on this story.
If you have a news story or tip-off, get in touch at editorial@sprinter.com.au.
Sign up to the Sprinter newsletter