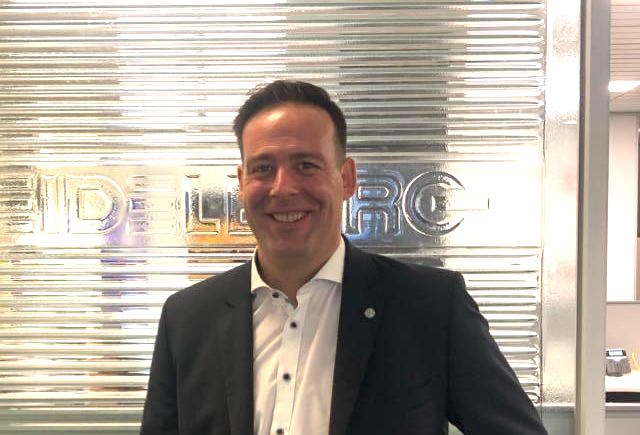
This article was first published in the November 2020 issue of AP – By Heidelberg A/NZ labels and Prinect solutions sales manager Dierk Wissmann
Prepress functionality remains one important module of an integrated print production workflow. However, the basic prepress market focusing on just prepress functionality is under pressure in terms of volume as well as price as printers are looking for complete integrated workflows covering prepress for offset and digital printing, pressroom, finishing (including delivery), and the integration of an MIS solution.
Industry surveys indicate that investments in workflow software has top priority for printers to boost productivity in modern print production with automated or navigated printing in digital and offset. Reliable platesetters and high-quality stable plates are required as they build the foundation for a high performance and reliable print production.
With the largest workflow R&D force in the industry, Heidelberg continues to lead with the Prinect Production Manager as the only supplier offering and continuing to develop an integrated print production workflow from prepress, press to finishing.
In addition, the Prinect Business Manager can be added as a MIS solution, making the Smart Print Shop workflow complete. Only Heidelberg offers the market such a complete workflow portfolio supported by one supplier.
Heidelberg has reacted on developments early with the Prinect offering.Today, modern subscription and volume-based workflow offerings make integrated workflow technology affordable to all market segments – from largerand smaller printers for commercial, as well as packaging and label segments.
Prepress beefs up a company’s offerings as Prinect as well as other modern prepress and workflow solution provide the required prepress functionality. The focus shifts more towards automation, including gang automation and customer integration via modern portal technologies.
Reducing the manual touchpoints, especially for standard jobs, is vital to stay profitable in a highly competitive market. Best-in-class customer service with 24/7 access and high speed, easy to work with portal and communication tools are mandatory and standard functionality of Heidelberg’s Prinect Production Manager offering.
Heidelberg has led the focus on integrated print production, allowing users to store and reuse data throughout the production process. The newest development with the Prinect Production Manager brings all required software modules together into one solution.
Starting with data directly entered by the customer, an automated print production is triggered with potentially zero touchpoints in prepress. In addition, data is used to improve the sequencing of print production, significantly increasing the overall equipment effectiveness in print production as change-over times between jobs are significantly reduced.
All of this supports the required productivity increase to stay competitive. In addition, the ability to drive offset as well as digital print production in a single job, out of the same workflow, is mandatory and a key feature of the Prinect Production Manager. This eliminates the need of two parallel workflows with its double costs.
The result of an automated Smart Print Shop Production is astonishing. In numerous cases, printers have doubled their good sheet production per hour as well as reduced costs. This has led to a significant reduction in cost per page, allowing printers to react differently to market developments.
As such, prepress offers the market value as high end print features like coating, spot varnishing and foiling provide the possibility for higher margin. They require special software tools and machines not every printer has.
But the top growth opportunity is in the packaging market segment. Even through the COVID crisis, the packaging and labels market continues its growth path. Modern prepress and print production workflows must allow for the easy addition of required packaging and label functionality with hardly any additional costs. This allows commercial printers to test the market and offer new products, which leads to better margins.
However, within this segment is the need to improve productivity as run lengths reduce. Thus, the functionality of a highly automated Smart Print Shop production is also required for the packaging and labels market.
The industry should also prepare itself for a future where modern prepress and print production workflow solutions support prepress operators, allowing them to eliminate simple, standard tasks which improve productivity drastically.
Prepress operators can then focus more on complex high-end print jobs, and the amount of jobs requiring manual intervention will decrease. In addition, I expect that more of the required functionality, especially automation, will be provided by cloud-based systems using latest workflow technology in future, including artificial intelligence to further improve speeds, errorless production and costs.
Those companies that embrace the changes will be among the winners in a competitive market.
Comment below to have your say on this story.
If you have a news story or tip-off, get in touch at editorial@sprinter.com.au.
Sign up to the Sprinter newsletter