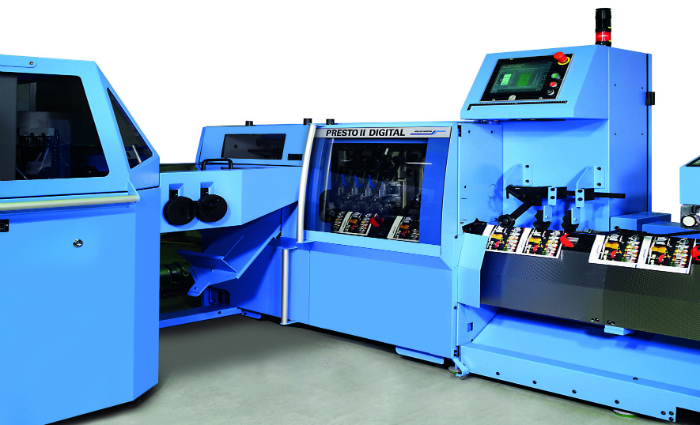
AUTOBOND SUV 52
Autobond’s SUV 52 spot UV machine, distributed in Australia by Graph-Pak, will suit printers who currently outsource their spot UV work. It provides an opportunity to bring revenue inhouse and build commercial growth, while providing greater job control for work such as magazine covers, flyers, folders, business cards and pharmaceutical packaging.
The SUV 52 uses a row of seven inkjet print heads to digitally print drop-on-demand LED curable spot UV varnish onto matte OPP laminated sheets. It consists of an Autobond conveyor table built 2.5 metres long, 1.1 metres tall and 1.02 metres wide. The conveyor table is split into two sections; the first half consists of a series of angled side-shift rollers which move the sheets into a side-lay for registration (similar to a folding machine), and the second half consists of a driven vacuum belt to hold sheets completely flat.
A high-speed electronic contrast sensor detects a mark or line printed on the front of the sheet, which registers the speed and distance it is travelling in relation to where the inkjet heads are to print the varnish. When the sheets are flat, the inkjet print head bar prints the varnish in the correct pre-determined area of the sheets.
Makeready is as little as one sheet because an 8-bit 360dpi greyscale bitmap (BMP) image file of the print job, formatted for Microsoft Windows, is downloaded to the software controlling the inkjet print heads. The sheets then continue along the vacuum feed table and pass under a low energy, cold curing, ozone-free LED lamp which cures the varnish, and finally delivers the sheets into the stacker.
The maximum speed at 360dpi is 36 metres per minute, or 12 metres per minute at 720dpi.
The Autobond SUV range can be upgraded in the future, in line with requirements. This machine comes with an installation and training package by a factory-trained engineer, and annual services are available. It sells for $330,000 + GST for the standard model, delivered and installed.
DFC DIGITAL FLEXO CUT The DFC represents a major breakthrough in applications such as die cutting, kiss cutting, perforation, embossing and creasing. Previously these have only been possible inline with sheetfeed offset presses. The DFC is a standalone machine with all the advantages of the inline technology but gives the user full flexibility on different formats and materials, even on small runs.
Due to its short set-up time, the DFC is particularly suited for small to medium and frequently changing running lengths in digital or offset printing. Its versatility enables print shops to process even highly specialised jobs at a profit.
With a maximum sheet size of 500mm by 430mm it is suited to many applications including presentation folders, CD covers, product display boxes, business card boxes, and the list goes on.
The flexible dies are supplied in Australia through Melbourne-based company Rotometrics, which worked closely with Nagel in Germany in developing the dies specific to this machine.
DUPLO DC646 SLITTER, CUTTER, CREASER
Duplo’s new DC-646 slitter, cutter and creaser is an upgrade of the previous, and successful, DC-645.
The new DC-646 offers additional features for 21-up business card cutting (in fact, it could cut more on longer sheets). It provides creasing, scoring and perforation along and across the sheet, and offers time or strike perforation across and along the sheet.
The DC-646 offers a plethora of functions including slitting, cutting, creasing, scoring, perforating, and strike/time perforating. Its cutting and creasing are comparable to any other device in the market, but with greater accuracy, says Australian distributor Neopost.
Current users handle business cards, stationery, menus, coupons and covers for stitchers and perfect binding. Typical users include copy shops, commercial mail houses, commercial printers converting to digital, as well as boutique print shops offering wedding stationery, and so on.
The Duplo DC-646 in standard format will handle many jobs, while the perforation, scoring and strike/time features are add-on modules. It reduces the need for a staff member to stand by the guillotine or creasing or perforation device, even compared with a cylinder setup. Saved job functions mean immediate job set-up.
The machine’s benefits include reduced wastage, and an improved registration mark reader means faster reading to detect the start of the job and immediate correction for digital shift. The DC-646 also allows printers to reduce their volume of outsourcing as it offers many features in the one investment.
Neopost offers delivery, installation and training with all machines. The company also offers up to five years onsite maintenance, which includes parts, labour and additional training to suit growing businesses.
Neopost also offers finance through Neopost Finance. The Duplo DC-646 has not yet been released in Australia, so pricing has yet to be confirmed.
FERAG UNIDRUM
Ferag has installed new UniDrum technology at Dutch print facility Senefelder Misset in Doetinchem. It is a prime example of how Ferag’s bindery technology is capable of handling large volume work automatically.
Senefelder Misset uses the gatherer-stitcher drum to produce the same magazine volumes that would normally require two conventional gatherer-stitchers, with reserve capacity still available. The company produces magazines with circulations between 10,000 and 180,000 copies and paginations between 60 and 132 on 16- and 72-page heatset machines.
The UniDrum set-up uses the PreTronic CV preset system, and is capable of handling production speeds of 40,000 copies an hour. Senefelder Misset claims it is boosting productivity, lowering costs per copy, and is further sharpening its competitive edge in the low circulation segment.
CEO Ronald van Rossum says, “In 2012 we began a feasibility study. Among the details checked by our team were the financial considerations, the workflow, and also production output. The excellent results led to a unanimous decision in favour of this system.”
The line secures the process in inline mode throughout, from gathering the folded signatures to readying the magazines on pallets for dispatch. Directly after the UniDrum comes the three-side trim in a single-rotor SNT-50 trimming drum. Like the UniDrum, when changing jobs all presets are fully automatic in the trimming drum, thanks to the PreTronic CV.
HEIDELBERG ST500 STITCHER
According to Heidelberg, the all new ST500 stitching machine, and the new smaller ST200, are in a class of their own. They offer speed, accuracy, short makeready times and versatility, says the company.
The ST500 offers features such as new servo drive technology and collating of folded sections for perfect binding.
The stitchers can be configured with a range of feeders – vertical for general commercial folded sections, horizontal for lightweight folded sections, cover, hand inserting and log feeders. The new platform of stitchers has been designed so that each machine can be individually built to meet each print business’s requirements.
The new ST500 offers quality control checks via product thickness, stitch and width control, plus fast change stitching heads, along with a range of different levels of automation. Automated trimmer, stitching unit and automated feeders are just a few options available with these machines.
Printers considering buying a Heidelberg ST500 or ST200 will be backed by Heidelberg Service. Heidelberg has trained service technicians available across Australia and New Zealand, and can tailor a customised after sales support programme to fit individual needs. Finance is also available on purchases through Heidelberg Print Finance, subject to credit approval.
HOHNER DIGIFINISHER
Cyber Australia, distributor of the Hohner Digifinisher, says that it is ideally suited to printers who have recently invested in digital print engines to complement an existing litho department.
The Digifinisher is designed to tackle complex finishing jobs that require collation and binding of numerous pieces, with individual items different in size or content.
For example, it would suit printed personal accounts and reports for the financial market, with the need to combine personalised information which has been digitally printed in sequence, variable from person to person depending on the size of their investments and overall portfolio. One book may have 24 pages, the next eight, followed by a 36-pager, and so on. Each customer may have a six-page preface letter followed by a glossy cover. Cyber says The printer must have verification that each and every book, without fail, matches the personalised cover.
Another example is a security printer which has landed a contract to produce school examination papers. In this instance the documents are not printed on flat sheets, but on a continuous reel.
The brief says that each page must be personalised to each student. There are 30 pupils in year one, taking six subjects each. The number of pages for each pupil will vary depending on which subject he or she is taking. There may be 20 pupils in year two, taking five subjects, but their papers will contain more pages due to slightly more complex question papers. Eventually year six will have fewer students, but each one will have considerably more pages in each subject.
Such complex finishing problems can be tackled by investing in a Hohner Digifinisher, says Cyber.
This system is based around a Hohner HSB 8000 Saddlestitcher fed by either a flat sheet pile feeder or an optional continuous reel feeder. A number of barcode optical recognition systems are available to provide complete security.
Two-up production and hole punching inline are also options.
HORIZON BQ-280PUR PERFECT BINDER
Horizon’s BQ-280PUR Perfect Binder is specially designed to handle the requirements of digital print – with digital print friendly processing, quick set-up and changeover for shorter production runs, book-of-one capability, and even inline verification for document integrity.
The BQ-280 also uses environmentally-friendly PUR glue which meets the requirements of lay-flat binding for both offset and digital prints as well as coated stock.
The large colour touchscreen features intuitive icons for easy operation. Just input book block and cover information at the touchscreen for quick and automatic
setup, including carriage clamp, milling, glue tank, nipping and cover feeder.
Up to 200 jobs can be held in memory and locked for additional security. The automated, sensor-activated digital caliper system ensures consistent measurement of book block thickness every time, eliminating operator discrepancy.
Book thickness is automatically measured by placing the book block into the digital caliper. The caliper slides into position with no manual intervention and thickness data automatically begins set-up. It handles the production of digitally printed books, personalised photo books, smaller sample runs and other ultra short-run work.
It will handle book block sizes of minimum 135 by 105mm up to a maximum of 385 by 320mm, and book thickness of 1mm up to 51mm. Cover weight range for normal paper is 62 to 302gsm, and for coated paper is 105 to 349gsm. Cover pile height is up to a maximum of 70mm. Milling depth is up to a maximum of 4mm. Production speed is up to 500 cycles an hour.
JMD DIGITAL ROBOT 2000 AND IBIS SMARTBINDER LINE
The JMD Digital Robot 2000 is an inline PUR binder for sheet and web fed digital presses. It is capable of automatically feeding sheet cut or thread sealed digital book blocks.
The IBIS Smartbinder is an inline saddle stitch and thread seal binder for sheet and web fed digital presses.
When combined inline, this configuration allows automatic computer set-up of saddle, perfect PUR or thread seal PUR books from either sheet or web digital presses.
Both of these machines are available from Pressnet. According to the company, with this combination of machines the choice of binding is at every printer’s fingertips.
LAMINATION SYSTEMS Q LAM IRIS WF
With the experience of more than 20 years in the industry, Lamination Systems has released the Q Lam range of automated laminating machines for the digital and offset market.
The Q Lam Iris WF thermal lamination system is available in two widths – 520mm and 720mm. This single sided celloglazer also incorporates a pro de-curl system and is capable of high speed, fully automated laminating at up to 20 metres per minute.
Made in Europe with high quality components, the Q Lam IRIS 52 and 72 are equipped with an electronic servo-driven feeder for ease of set-up and advanced roller surface heating for a smooth and consistent finish.
The IRIS requires minimal adjustments, all of which can be done by touchscreen.
Also available in Lamination Systems’ range is the Mini Bond Desktop Celloglazer, an entry level machine that allows a single operator to celloglaze both digital and offset print up to 320mm by 450mm in size.
Unlike other desktop laminators, the MiniBond applies maximum heat and pressure through a large diameter chromed heating roller (similar to a commercial machine) as well as an accurate feed belt system and built-in rewind unit for single sided laminating.
With over 150 units sold in Australia since its introduction in 2008, the Mini Bond has become a popular laminating solution for copy shops and digital printers.
It is priced at under $3,000, and produces a laminated finish comparable with more expensive machines.
MBO M80 FOLDER
MBO is introducing the new M80 modular folding machine at China Print 2014.
With its modular design technology the M80 can be reconfigured after purchase to operate as a buckle folding machine or a combination folding machine. This gives printers the freedom to add or change components to meet whatever demands the market brings, such as adding buckles or knife folds later without the need to buy another folder. It also means that printers can afford to buy the basic fold configuration today.
The M80 can endure continuous use with reliability and precision. With an infeed width of 83cm and production speed capability of up to 230 metres per minute the M80 offers true productivity.
The new M1 machine control is user friendly due to its intuitive touchscreen, so it can easily be operated with minimal training.
MBO has manufactured products for the printing industry for over 40 years, and boasts a reliable name in bookbinding and post press finishing. MBO products are distributed in Australia by Ferrostaal Australia.
MULLER MARTINI PRESTO II DIGITAL SADDLE STITCHER
Responding to diminishing run sizes for magazines, periodicals and brochures combined with increasing product variety and demand for shorter processing times, finishing giant Muller Martini is focusing increasingly on digital printing in the field of saddle stitching.
Muller Martini says its Presto II Digital saddle stitcher is designed for small and medium-sized enterprises seeking to be fit for the future. “Roman Beeler from Muller Martini in Australia says, “With its modular design, the Presto II Digital is the ideal saddle stitcher both for graphic arts businesses already printing digitally and for those that are still printing conventionally but intend to enter digital printing in the future.”
The Presto II Digital is quick and easy to set up, making job changeovers in a matter of minutes. It has a maximum operating speed of 9000 cycles per hour where a single signature is being stitched, but for most customers the running speed is of secondary importance. Efficient job changeover and reliability are greater concerns, and in any case speed is governed by a combination of product thickness and number of signatures. It can handle job sizes from 93 by 60 mm up to just over A4 size. A4 landscape is also possible.
The Presto II Digital is set up largely using simple touchscreen controls (universal across the Muller Martini product range), with screens for general job data and signature definition. A series of handles are used for setting the signature assignments, trimming parameters and delivery, guided by the settings produced by the computer.
The position of the stitching heads is also set by hand, according to the computer settings. However, the yoke timing, gathering chain, trimmer and feeders are automatically synchronised. Regular jobs can be stored in the software.
There is a wide variety of possible configurations for the saddle stitcher, depending on a customer’s needs. Inline MBO folding and plow folding (with static eliminator) can be integrated, Asir 3 barcode reading can be used to track jobs being processed; up to six signature feeders and three cover feeders can be used, and various additional finishing processes, such as die-cutting and hole punching can also be integrated into the system.
PITNEY BOWES DI950
The Pitney Bowes DI950 simplifies one of the challenges in any print-to-mail process – getting the mail piece into the envelope quickly and accurately. Mail fulfilment enables businesses to increase margins by offering customers more.
The DI950 is a modular and scalable solution that offers production inserting capabilities with a small base footprint of 2,260mm. It can handle both straightforward and more complex transactional mail such as folded or unfolded multi-page statements, bills and cheques or promotional material with multiple inserts.
The system accepts letter-sized and flat envelopes in a wide range of sizes, and even permits multiple folded sets into one envelope.
As customer volumes increase, additional modules such as output stackers and high-capacity sheet feeders can be added.
The DI950 is designed to keep running, so users can reload their customers’ media on-the-fly, or link multiple feeders to increase capacity and reduce time spent loading material. It can handle up to 5,400 mail pieces per hour.
With sophisticated barcode scanning, the system runs jobs with variable pages securely, directly eliminating costly manual sorting by page count.
But the company says sophisticated doesn’t have to mean complicated; it says the PacPilot user interface and control panel is easy to use.
Available in 23 languages, the PacPilot uses full-colour graphics and text to show where and how to load materials. Users can save up to 24 pre-programmed jobs for common customer requests, or use the Swift Start feature that senses how to run a job based on the materials that have been loaded, saving on operator programming time.
Pitney Bowes offers mail fulfilment consulting, onsite product training, professional installation and full-service equipment maintenance agreements with guaranteed response times. Pitney Bowes Global Financial Services provides printers with several financing options to fit their budget.
PLOCKMATIC CST CREASE SIDE TRIMMER
Plockmatic’s CST trimmer is a new addition to the System 300 full-bleed booklet making system, which was first shown in Australia at the Fuji Xerox Australia booth at PacPrint13 in Melbourne.
The CST Crease Side Trimmer caters to demand from the digital print market to expand the System 300 – consisting of the ACF 510, BM 2000(S), TR 2000 and SQF 2000 – to deliver creased and full-bleed booklets directly from media sizes such as SRA3, straight from the printer. Creasing of the cover is a requirement for virtually all digital colour applications.
According to Plockmatic, adding the CST to the company’s booklet making system greatly expands its market opportunities. The Plockmatic CST attaches to the BM 2000 and BM 2000S booklet makers, and both the ACF 510 and VF 1008 ME feeders are supported by the CST.
The CST has a host of features which are controlled from the user interface on the booklet maker itself.
The Bleed Trim function trims the top and bottom edges from each sheet, enabling full bleed jobs. Sheets are precision trimmed one by one using rotating blades. Trim waste transport enables long unattended runs.
The Crease function automatically cuts the risk of cracking on the spine. The dual tool design can be set to either fine or coarse, depending on the media being used, via the user interface.
Active anti-static bars are available as an option to overcome the high static charge that may occur in some environments.
Plockmatic offline products are distributed by Fuji Xerox Supplies in Australia and Fuji Xerox New Zealand.
RENZ GMP PROTOPIC III 540 LAMINATING SYSTEMS
Renz Australia has launched a new GMP Protopic III laminator series to produce a range of cost effective finishes that will add value to print jobs. With the market trending towards shorter print runs, produced on digital machines, the challenge for printers is to add value to their work while improving their bottom line.
The new GMP Protopic III 540 series is ideally suited to small, medium and large operations, and can provide digital printers with the capability to produce single and double-sided laminates and a range of effects like embossing, spot varnishing and metallic foiling.
In addition to special effects it is possible to upgrade from a semi-automatic model to a fully automatic version by adding an optional modular vacuum stream feeder, auto-stacker or an automatic cutter on double-sided models to increase productivity as the business grows.
Standard on all models are rewind capabilities to support the digital sleeking process. Digital sleeking, a patented technology exclusive to GMP, uses specialty adhesives that only bond with ink or toner to provide spot varnish effects, metallic foiling or holographic effects, and UV coatings for short to medium runs. The different finishes include gloss, matte, hologram and a range of coloured metallic foils, as well as the traditional silver and gold.
Dual roller models also provide the ability to produce embossed textures, including a silver halide replacement effect that can be used as an alternative to traditional photo processing. Other finishes include linen, leather, sparkler, silk and fine texture.
Duplex models provide the capability for double-sided lamination in a single pass and can be optioned with an easy cutter that will automatically trim the encapsulated sheets.
The Protopic III 540 range of machines is reliable and straightforward to use.
The standard installation package from Renz includes full operator training backed up with a national support network for technical service and consumables through the company’s state branch offices and authorised dealers.
These machines range from $24,000 to $55,000 depending on model and options, and the company says finance is available at competitive rates.
RIGO LAMIBIND 340 PUR BINDER
Increasing adoption of digital printing in the commercial print sector has created a number of challenges in sourcing cost effective short run finishing solutions.
Fab Equipment has expanded its range of finishing systems with the introduction of its new 340 PUR binder, after the successful release of its bigger brothers, the Rigo Lamibind, Megabind and Perfect Binder 420 PUR binders.
The new model is designed to further reduce the entry price point for a professional semi-automatic PUR binder, ideally suited for very short runs of A4 and A3L size books.
Using a closed tank PUR system that also incorporates side glueing and spine glueing via nozzles, bind strength and quality are not compromised, says Fab, while also reducing the waste and clean-up time associated with open tank systems.
Features on the 340 PUR binder include a motorised clamp and automatic binding unit, a robust milling system with dust extraction and operator friendly touchscreen display.
The Rigo Lamibind 340 PUR binder is ideal for businesses looking for an entry level PUR binding system that, when compared with outsourcing alternatives, will reduce costs, improve turnaround times and increase profitability.
It is priced from under $40,000 + GST.
RILECART WIREBINDER 360
Rilecart wirebinding machines’ reputation has been reinforced with the success of the Wirebinder 360 semi-automatic wire binding machine.
Originally targeted at customers looking for a cost effective move from hand and desktop binding into semi-automatic binding, Rilecart says the WB360 quickly attracted interest in other areas as well, particularly for customers with larger, less flexible machines looking for quick, simple set-up for small jobs and for digital print applications where fast service is key.
This machine and its recently released larger stablemate, the Wirebinder 450, have the capacity to bind books and calendars using wire on spools over a full range of diameters from 3/16 inch to 1.25 inches, in sizes up to 360mm or 450mm long, and at speeds of 600 books per hour.
These machines have been designed to handle volume jobs using double loop wire on spools or cut length wires for quick production of small jobs or customer samples.
The new Wirebinder 450 can be supplied with a hanger feeder system for the production of calendars.
Signalling a further move into the digital market, Rilecart has added two new heavy duty desktop punching machines, the Diamond Punch and the Ultramac, which it says when combined with the Wirebinder machines offer a cost effective and productive entry level package for the digital market.
Ultramac is based on Rilecart’s Diamond desktop punch technology, including interchangeable punching dies, but with the added feature of automatic punched paper ejection from the machine into a stacking bin. This feature allows the operator to concentrate completely on the punching activity.
These new machines complement the existing broad range of Rilecart punching machines for wire, plastic coil, comb and universal binding.
Rilecart Binding Supplies’ Gary Disney is pleased with the acceptance of the Wirebinder 360 since its release in Australia.
“Wirebinder machines really sell themselves,” he says. “Customers are impressed with how simple they are to set up and operate, and the low price tag makes the investment easy to justify.”
THERMOTYPE TS2L MARK IV DIGITAL FINISHING MACHINE
According to Australian distributor Graph-Pak, the versatility of the TS2L programmable finishing machine means it can produce round corner products, inline slit, score, perforate, semi-slit, cross perforating, up and/or down creasing, die cutting, blind embossing, hole punching and bindery punching.
The Zip TS2L is a completely new design featuring a guillotine cutter and two cooling stations, as well as inline slitting, scoring, semi-slitting and perforating functions.
The TS2L offers simultaneous multi-function processing for business cards, forms, brochures, calendars, Christmas cards, door hangers, docket books, tab inserters, wobblers, stationery, photo books and more.
The TS2L can be continually upgraded and retrofitted to suit the growing demands of the business, and comes with an installation and training package by a factory trained engineer. Yearly services are available.
It costs $115,000 + GST for the standard model to be delivered and installed.
Comment below to have your say on this story.
If you have a news story or tip-off, get in touch at editorial@sprinter.com.au.
Sign up to the Sprinter newsletter