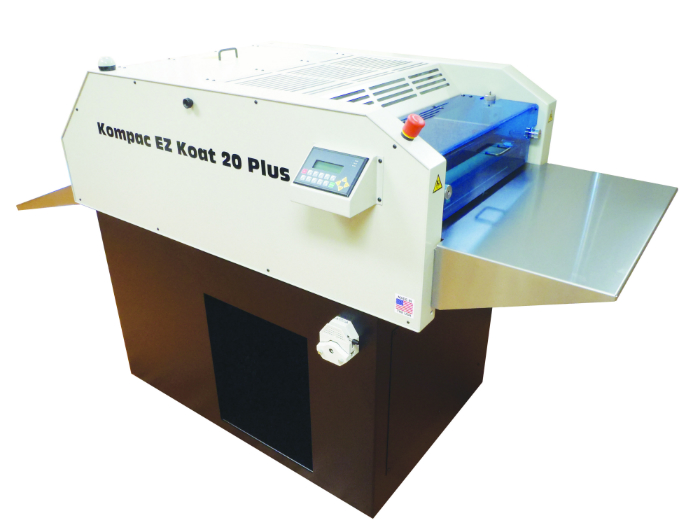
Duplo Spot UV Coater
The Duplo DDC-810 Digital Spot UV Coater offers printers the capability to enhance images with a layer of texture and depth. Using inkjet technology together with an ultra-violet lamp to instantly cure the UV varnish, the DDC-810 applies a gloss finish to defined areas of the substrate giving them more impact and appeal. A CCD camera, which automatically corrects for shrinkage, stretch and skew, along with registration marks ensures the accurate and precise alignment of the spot UV image onto the printed document.
Equipped with Duplo’s air suction feed system, the DDC-810 can process up to 21 ppm (ledger size) and 36 ppm (letter size). The unit features a dust roller, metal hydride lamp, ultrasonic double feed detection, fully automated head cleaning purge, and detection sensors for miss-feeds, ink attached, ink near empty, ink disposal tank full, cover open/closed, jam before and after UV lamp, and feed empty. It is easy to set up and operate, the DDC-810 is ideal for short to medium digital and offset medium jobs.
As printing methods become more varied, there is growing demand for binding with coated and digitally printed sheets. EVA hotmelt glue has difficulty binding coated stock firmly, and does not currently provide good spine flexibility and lay-back qualities. However, PUR hotmelt glue can provide adequate binding strength and a lay-flat quality for both offset and digital print on a wide range of paper stocks.It is sold through Neopost.
Horizon BQ-480
The Horizon BQ-480 features a higher level of automation, in addition to dimension based automation, the BQ-480 features customised automated setup accounting for paper type, signature vs. loose sheet, sewn book blocks, notch binding, and other key factors for higher quality with less effort. It also has a book of one production with maximum production speed of 800 books per hour for book of one production.
The production speed changes depending on thickness change from book to book. Its gentle boom delivery system is a book delivery mechanism delivers the book gently for high quality books, even with 65 mm thickness books or PUR bound books. The BQ-480 has a selection of glue types supporting both EVA hotmelt glue and PUR hotmelt glue. Two different tanks are available for each glue type.
In the book feeding section, a rigid clamping system holds the book block firmly in position during the milling and nipping process to produce a quality finished book. The safety beam ensures risk-free operation. The milling section powerful servo motor driving milling and notching mechanism mills the spine of a book block or signature for optimum glue penetration and adhesion.
Milling rotation speed can be adjusted automatically according to book thickness and custom template. Milling depth can be adjusted from 0 to 4 mm or 0” to 0.157”. Its glue tank section has dual application rollers and side gluing rollers ensuring superior glue application to the spine and excellent adhesion of the cover for consistent quality binding. Glue roller height, wiper opening and cut-off timing, scraper roller height, and side glue roller width are all automated.
The nipping section is a strong rigid nipping mechanism and positive jogging guarantees precise alignment of the cover to the book block and square spines. Nipping width, height, operating time and delay time are adjusted automatically according to book thickness. The cover registration section is used after transport to the nipping section, the cover is registered precisely with the fore edge guide and tail edge positioner. The system features various functions to improve production and quality.
Choose between input based pricing (labour, machine and materials), catalogue pricing or specific contract pricing per customer. The ability to use market driven pricing for your sell price while still maintaining actual costs.
A toolbox full of automation options to control your layouts, control margins and automate many of the mundane processes. Easily replicate all your current Excel based calculators within a centralised quoting environment.
The production management tools within printIQ focus on communicating information in real time to everyone within the factory. With tailor made views of a job for each department, we have delivered a tool that eliminates the in-trays, the talk and the re-work. PrintIQ in 3D separates the job from the estimate so you can freely update the production path without affecting your quote information.
Online production boards give you the full view of the floor regardless of where you are. The digital job bag manages the job in real time which in term feeds status updates back to the production board. Tablet optimisation to keep you moving. Time capture functionality directly from the job bag or Job Details screen. Customers can control and plan your work with multiple scheduling options. Switch production path and still retain details from previously executed processes.
Kompac EZ Flood Coating System
The Kompac EZ Koat product line is a small footprint flood coating and curing system capable of sheet fed or web applications running inline or offline with excellent UV/Aqueous Coating Quality in a Small Footprint.Digital UV Kompac Guarantees 25 per cent cost reduction over your ballast type UV system due to its digital UV system. You can fine tune the exact amount of UV power for each job with coating changes and clean-ups in two minutes or less.
Customers can also change from Primers to UV and/or UV to Aqueous in two minutes or less. Competitive coaters take 45 minutes to over one hour to change coating and typically waste more than a gallon of coating on each change.
Made in the USA, the Kompac EZ Koat is built for 24/7 operation. The company says EZ Koat is the only UV coating system to feature Digital UV. Environmentally friendly, digital UV replaces outdated and potentially hazardous ballast and mercury relay systems used in curing UV coatings. The EZ Koat is the only system that can successfully pre-coat using AQ safire coatings for Indigo Digital Presses, creating an opportunity to save money on expensive pre-coated stock.
An offline coating and curing system, providing a quick and easy way to apply UV, aqueous, primer and specialty coatings to a wide variety of substrates, either spot or flood. Whether paper or plastic; digital output or offset, each job will have the visual appeal, lasting durability, protection and rub resistant finish that customers expect.
Its features include an automatic double-sheet detector, stream feeder with continuous pre-load, removable cylinder grippers, a touch screen control panel, equipped with interlocking safety guards and E-stops, circumferential and lateral registration for accurate spot coating and flood and spot coat as well as spot not coat (allowing areas to be free of coating for variable data printing).
Includes Kompac Kwik Stack, an automated receding stacker, a Kwik release blanket bars (for fast job changes), auto coating level pump and sensor which automatically replenishes coating when it is low and a patented Kompac air delivery system providing a non-contact delivery of the coated sheet.
The Patented Kompac Coating System provides on the fly coating adjustments, produces the highest quality gloss and a perfect finish every time and it is easy to clean and change coatings. With the patented Kompac Vac and its environmentally friendly UV clean, coating change and clean takes five minutes. Perfect for medium to large offset printers, packaging, converters and Xeikon and other large digital presses.
Konica Minolta MGI 3D JetVarnish
Konica Minolta has a focus in postpress for digital which is about adding value, services and increasing the opportunity to generate client satisfaction that in turn translates to business growth. Konica Minolta’s MGI 3D JETvarnish EVO offerings can produce a traditional 2D Spot UV effect, a raised 3D Spot UV effect, and a hot stamp foil all on one unit. They are available in four different widths (364mm, 520mm, 640mm, 750mm) to suit different sheet sizes and at a length of 1200mm.
The demand for differentiation by commercial printing clients is on the increase.
They have a need to achieve greater results from their marketing spend and to separate themselves from their competition. Postpress functions such as Spot UV and foiling effects have been a means to achieve this in the print industry for some time. Now the MGI 3D JETvarnish EVO brings this postpress offering via a digital workflow. Along with it comes all the advantages of digital printing such as shorter runs, variable data and versioning, no costly dies or make-ready, the ability to make last minute changes and ease of use.
At PacPrint 2017, Konica Minolta announced the official launch of the MGI 3D JETvarnish. The MGI 3D JETvarnish has many new advances redefining what digital spot UV and foiling can offer its users in postpress workflows to add new revenue streams. For the commercial printer that installs an MGI EVO, they have the opportunity of in field scalability.
They can upgrade from EVO 52 (520mm) to an EVO 65 or 75 according to their growth, and how their business changes. This maximises the lifecycle of the equipment as well as increases productivity.
The raised Spot UV and foil effects can be produced at a height of 200micron. This feature alone opens discussions with clients to produce high-class print work. Around the globe, users of the MGI EVO technology are opening new markets for example; braille, short run embossed covers, point of sale material or targeted marketing pieces.
A recent infoTrends study commissioned late 2016 “Beyond CMYK: The Use of Special Effects in Digital Printing” highlights the value of offering postpress special effects. Konica Minolta believes the return on investment speaks for itself.
Morgana Digibook PUR Perfect Binder
Over the past 10 years Morgana has seen a shift by the trade houses towards PUR binding to reduce uncertainty of glue binding reacting against varnishes, toners and varying paper types. Unfortunately, PUR binding also comes with an increase in cost for the print buyer due in part to cost of long make ready, wash ups and glue wastage for each shift of PUR binding.
These issues have been addressed by Morgana within the Digibook range. Morgana have developed a range of PUR binders which are ready to use in 25 minutes from first start up and are cleaned in less than five minutes with almost zero glue wastage.
This is only possible through a closed glue tank utilising a slot applicator to deliver glue to the book on demand. Morgana has put a lot of R&D into this and have seven patents on the glue system alone. Morgana says the simplicity of this system means that any print shop or finishing house can perfect bind books on demand each day or as required by the customers.
With Morgana it is feasible to bind 10 books in the morning then clean up and then if you receive another order the same day, simply heat the machine back up and bind more books.
Morgana Digibook range covers four levels of production with entry level being 150 books per hour through 200 to 300 finishing at 450 books per hour. Digibook 150 and Digibook 200 are so versatile they plug into standard electrical power points.
The closed glue system allows for the machines to be operated without the need to extract glue fumes, which means the machines can be operated in almost any location.
Rollem Insignia6
Rollem International presents the Insignia6 sheet-fed flexo-magnetic rotary die cutter with a versatile sheet capacity of 20 x 20’.
Offering die cutting, kiss cutting, cut scoring, creasing, perforating and hole punching all in one pass, the Insignia6 enables maximum utilisation of sheet imposition with the ability to feed sheets either portrait or landscape.
The Insignia Series has been widely adopted by commercial and package printers alike as it offers easy entry in to the growing packaging segment of the printing industry.
Its ability to convert an extensive range of stocks extending beyond paper and board including PVC, PET, plastic, vinyl, magnets and even lightweight aluminium – opening it up to a broad product spectrum. It also handles stock weights up to 26 pt. thickness, ideal for folded carton products.
Insignia’s quick set-up and easy changeover make it ideal for digital printers offering customised consumer products such as folded cartons for cosmetics, soaps, and craft boxes. Beverage labels, retail hang tags, and computer component inlays are also ideally suited for this model.
Insignia is now offered in three sizes: Insignia5 20×15”, Insignia6 20×20” and the Insignia7 30×24”. Insignia uses a full press style register system to guarantee 100% sheet-to- sheet registration. With a robust, production level design, these machines can run up to 5,000 sheets per hour. For complete automation, Insignia is offered with an in-line folder/gluer unit to deliver finished, glued products, in one process.
The Insignia die cutter offers a wealth of value added processes in an economical, easy to use machine, designed and manufactured in the US. “We are seeing customers from a broad range of sectors including commercial, packaging, photographical and industrial companies. Some seeking to eliminate out-sourcing and others with legacy machinery who are looking for shorter run, easy to operate alternatives,” says Susan Corwin, marketing manager. We are pleased to be represented in Australia by Graph-Pak.
Insignia is not a ‘one size fits all’ machine. Printers have the choice of configuring the Insignia with Single or Dual magnetic cylinders, Bearered vs. Non-Bearered cylinders, and multiple delivery options to meet their production requirements.
Comment below to have your say on this story.
If you have a news story or tip-off, get in touch at editorial@sprinter.com.au.
Sign up to the Sprinter newsletter